Machining Titanium
Updated : Jun. 25, 2025Titanium is widely used in high-end manufacturing fields such as aerospace, medical, energy, and automobiles, but it is also recognized as one of the most difficult metal materials to process. Compared with traditional metals, titanium has low thermal conductivity, high strength, and low elastic modulus, which bring a series of challenges during processing.
During machining, titanium can easily cause the temperature in the cutting area to rise rapidly, resulting in increased tool wear or even failure; the toughness of the material itself can easily cause machining vibration and deformation, especially in thin-walled parts and parts with complex curved surfaces. In addition, titanium has a strong affinity for tool materials, and problems such as tool sticking and chipping often occur, seriously affecting the surface quality and dimensional accuracy of the machining.
Because of this, titanium processing has always been a technical barrier in modern manufacturing, and has therefore become a focal topic of continuous attention and research in the industry.
Introduction to titanium alloy and its processing value
Like all other metals, titanium has many different alloys, each with its own unique properties and behavior. Here is a summary of the different types:
Pure Titanium | Alpha Alloy | Beta Alloy | mix |
As the name implies, pure titanium does not contain any alloying elements and is the easiest type of titanium to machine. | This refers to titanium alloys that contain aluminum, oxygen and/or nitrogen. | This refers to titanium alloys that contain molybdenum, iron, vanadium, chromium and/or manganese. | This is a mixture of alpha titanium alloy and beta titanium alloy. |
Despite its high price and difficulty in processing, titanium is still widely used in various industries, mainly due to its following key performance advantages:
Extremely high strength-to-weight ratio: While ensuring sufficient strength, it significantly reduces the weight of the structure, making it an ideal material for the aerospace and racing industries.
Excellent corrosion resistance: It is not easily corroded in seawater, high temperature and strong acid environment after long-term use, and is widely used in marine equipment, chemical heat exchangers, etc.
Excellent biocompatibility: It is not easy to cause human rejection reaction and is the preferred metal material for orthopedic implants and dental structural parts.
Good high temperature resistance: Some titanium alloys can still maintain structural stability and mechanical properties in high temperature environments, and are important materials for engines and hot end components.
Why is titanium alloy difficult to process?
Titanium alloy is a notoriously difficult material to machine and is very sensitive to many factors. Listed below are some of the main challenges in machining titanium alloys.
-
Complex Tool Path Design
The tool should stay engaged with the workpiece to avoid sudden cuts. Trochoidal paths and arc entry/exit help reduce heat and tool wear.
-
Heat Is Difficult to Release
Titanium’s poor thermal conductivity causes heat buildup at the tool, leading to rapid wear. High coolant flow is needed to cool and remove chips.
-
High Coolant Demand
In turning, coolant pressure and injection position must be precise. Improper high-pressure cooling may cause surface redeposition.
-
Difficulty in Clamping Workpieces
Titanium alloy parts are often thin in structure and low in rigidity, and custom fixtures are often required to stabilize the workpiece, prevent vibration, and improve cutting accuracy.
-
Strict Tool Requirements
Carbide tools with PVD coatings, such as TiAlN coatings, must be used. Titanium is very elastic, so the tool must be sharp to avoid passivation that causes vibration and surface friction.
-
Difficult chip control
Titanium tends to form long chips that harm tools and scratch workpieces. Chip-breaking tools and paths are preferred to produce short, thick chips.
-
High Machine Performance
Titanium machining demands rigid machines with high spindle torque to ensure low-speed, stable, and vibration-free operation.
-
Obvious Work Hardening
Titanium hardens during machining, accelerating tool wear. Constant feed helps limit hardening and maintain cutting efficiency.
-
Increasing Feed Rate Is Beneficial
Properly increasing the feed speed can shorten the tool's residence time in a single area, reduce thermal effects, and extend tool life.
Common processing technology and technical requirements of titanium alloys
The processing of titanium alloys is not only challenging but also involves complicated process steps. According to the product structure and performance requirements, the commonly used titanium processing technologies include milling, turning, drilling, grinding, laser processing, etc. The following are the characteristics and technical points of each process:
Milling
Milling is one of the most common processes in titanium machining. Due to the poor thermal conductivity and high elasticity of titanium, chatter and heat accumulation are very likely to occur during milling. It is recommended to adopt a low speed, high feed strategy, with a high rigidity tool system, and supplemented by high pressure cooling to extend tool life.
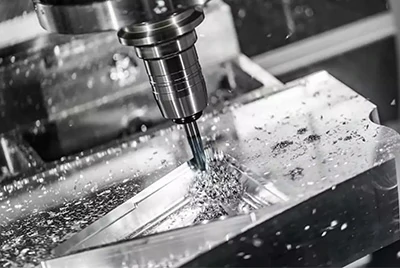
Key technical points:
- The tool requires high rigidity and sharp cutting edge
- Tool paths need to be optimized to avoid intermittent cutting
- It is recommended to use TiAlN coated carbide tools
Turning
When turning titanium alloys, the tool load is large and the chips stick severely. High cutting temperatures can easily lead to tool burns. The coolant must be precisely positioned and the injection pressure must be high enough to ensure stable turning.
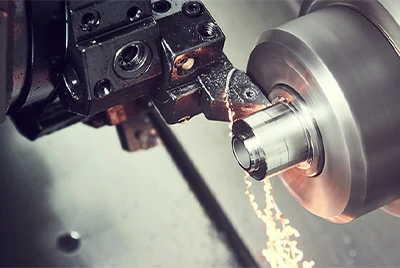
Key technical points:
- Precisely control cutting parameters to avoid work hardening
- Turning tools need to have good heat resistance
- The tool angle should be conducive to chip breaking
Drilling
Drilling titanium alloy is one of the most challenging processes. The main problems are that the drill wears quickly, the hole wall is easily heated and deformed, and the chips are easily entangled and blocked. Step drills, short drills and internal coolant structure drills are often used to alleviate the problems.
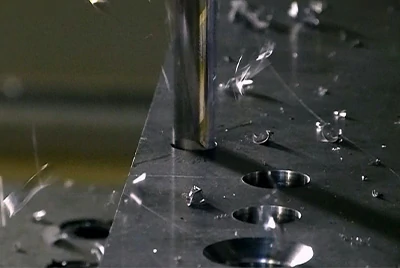
Key technical points:
- Prefer carbide drills with internal cooling
- Adopt a lower speed, higher feed strategy
- Continuous chip removal must be maintained
Grinding
Used for surface finishing and dimensional accuracy of titanium alloy parts. The low thermal conductivity of titanium makes it difficult to dissipate grinding heat, and the workpiece surface is prone to burns and deformation.
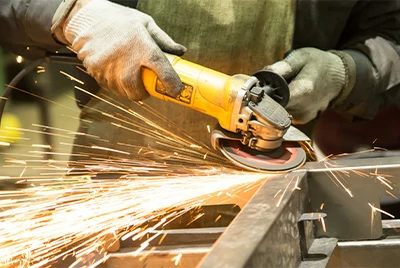
Key technical points:
- Using special titanium abrasive and high hardness grinding wheel
- Cooling must be sufficient, otherwise grinding cracks are likely to occur
- The cutting depth should be shallow to avoid local high temperature
Laser Cutting / Welding
Suitable for cutting complex contours or welding titanium alloys. Titanium is extremely sensitive to oxygen, and laser processing must be carried out in a protective atmosphere, especially during welding.
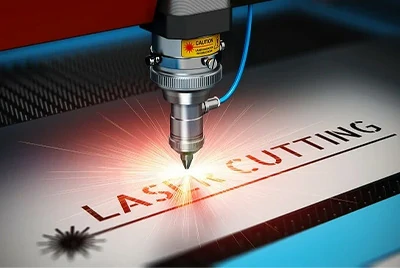
Key technical points:
- High-purity argon protection is required during cutting or welding
- Beam parameters need to be finely controlled to prevent overburning
- The heat affected zone needs secondary treatment to eliminate micro cracks
Titanium alloy processing solutions: meeting the needs of different industries
Titanium alloys are widely used in many industries. Each industry has different requirements for titanium alloy parts. We provide customized titanium alloy processing services according to the specific needs of each industry. The following are the titanium alloy processing solutions we provide for several key industries, and introduce the commonly used processing technologies in each industry.
Aerospace Industry
Titanium alloys are mainly used in aerospace for engine components, aircraft structural parts, turbine blades, etc. Since these components usually require high strength, high temperature resistance and corrosion resistance, we use advanced processing technology to ensure the stable performance of the parts.
Commonly used titanium alloy processing technologies:
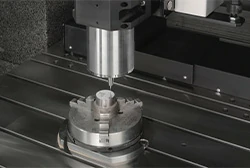
Precision Milling
High-precision cutting ensures the strength and corrosion resistance of parts.
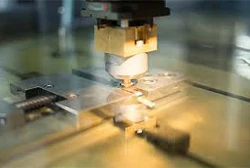
Electrical Discharge Machining (EDM)
Titanium welding ensures strong, sealed structural components.
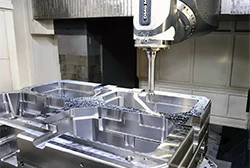
CNC machining
Surface anodizing enhances corrosion resistance and extends service life.
Chalcotitanium's aerospace processing service advantages:
- High rigidity machine tools and cutting tools reduce vibration and improve machining accuracy
- Customized processing solutions to meet different titanium alloy types and complex structure requirements
Medical industry
Titanium alloys are widely used in medical applications such as orthopedic implants and dental parts due to their excellent biocompatibility and corrosion resistance. We provide precision titanium alloy parts processing for the medical industry, ensuring compliance with strict quality standards such as ISO 13485.
Commonly used titanium alloy processing technologies:
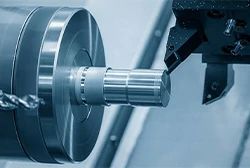
Precision turning and milling
Used in the manufacture of medical implants and surgical instruments to ensure smooth surfaces and precise dimensions
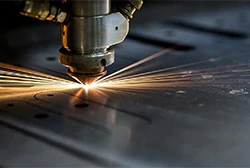
Laser cutting
Used for precise cutting of small apertures and complex shapes, often used in implant processing
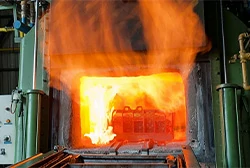
Heat treatment
Improving the strength and corrosion resistance of titanium alloys to ensure long-term stability of medical devices
Chalcotitanium medical field technical processing advantages
- Strict quality control system ensures that each part meets international medical standards
- Customized processing technology to meet individual needs and highly precise dimensional requirements
Automotive industry
In the automotive industry, titanium alloys are often used in racing parts, engine accessories and lightweight parts for high-performance cars. The titanium alloy processing services we provide focus on high-strength, low-weight design to improve automotive performance and safety.
Commonly used titanium alloy processing technologies:
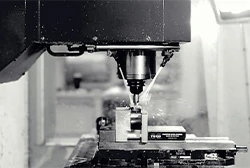
CNC Milling
High-strength automotive parts are processed through efficient CNC milling technology.
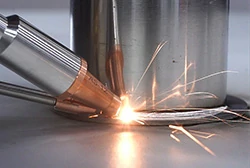
Laser welding
Used for welding high-strength automotive parts to ensure the integrity and durability of the welded parts.
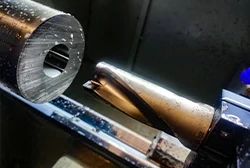
Deep hole processing
Specially used for processing deep holes and small channels in automobile engine parts.
Chalcotitanium's technical service advantages in the automotive field:
- Quick response and efficient production ensure delivery of large orders in a short time
- High-precision processing to ensure the strength and lightweight requirements of parts
Energy and offshore engineering industry
The excellent corrosion resistance of titanium alloys makes them an important material in the energy and offshore industries, especially in offshore platform components, heat exchangers and oil and gas equipment. We provide titanium alloy processing services with high reliability and corrosion resistance for these industries.
Commonly used titanium alloy processing technologies:
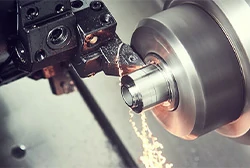
Cutting
High-precision cutting ensures the strength and corrosion resistance of parts.
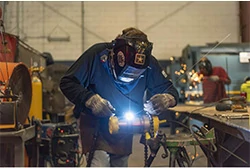
Welding Technology
Titanium alloy welding technology is used to manufacture complex structural components to ensure their durability and sealing.
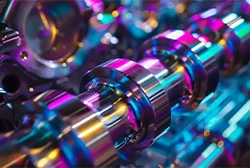
Surface treatment
Through processes such as surface anodizing, the corrosion resistance of parts is improved and the service life is extended.
Chalcotitanium's technical service advantages in energy and offshore engineering industries
- Provide high temperature resistant and corrosion resistant titanium alloy materials to adapt to extreme environments
- Strong welding and heat treatment capabilities ensure long-term use of parts in marine environments
Choose Chalcotitanium—— One-stop titanium alloy material and processing solution provider
The selection of titanium alloy is just the beginning. The subsequent processing and treatment often determine the performance and use effect of parts. Chalcotitanium has not only been deeply involved in titanium alloy materials for many years, but also established a mature production system in titanium alloy precision processing, covering key links such as turning, milling, drilling, welding, heat treatment, precision cleaning and surface treatment. We provide one-stop services from material to finished product delivery for a number of high-standard industries such as aerospace, medical equipment, automobiles, and energy equipment, helping customers save coordination costs and improve delivery efficiency.
We have the following processing advantages:
- High-precision processing capability: Equipped with five-axis CNC machine tools, precision grinders and other equipment, it can achieve a tolerance control of ±0.01 mm, meeting the strict requirements of high-end structural parts for shape and position accuracy.
- Complex parts solutions: We specialize in titanium alloy processing of thin-walled parts, special-shaped parts, and deep-cavity structures, and are equipped with multi-axis clamping tooling and vibration-reducing tool strategies.
- Highly stable production process: The entire process from raw material preparation to finishing and surface treatment is controlled to ensure consistency and batch stability.
- Process customization and collaborative development: We can provide process optimization suggestions and joint development services based on customer drawings and performance requirements, especially for projects with a high degree of customization such as medical implants and aerospace structures.
- Integrated quality management system: ISO quality standards and industry-specific specifications (such as AS9100, ISO 13485 and other project management models) are implemented throughout the entire process to ensure the process traceability and safety of the final product.
By integrating material supply and processing services, we can more efficiently control delivery time and cost while ensuring that product performance meets the requirements of end-use. For customers, choosing Chalcotitanium is not just choosing titanium itself, but choosing a reliable partner to work together to achieve high-quality implementation of difficult parts from drawings to physical objects.