Titanium Corrosion Resistance
Updated : Jul. 9, 2025Among many metal materials, titanium stands out for its excellent corrosion resistance. Whether in a high-salinity marine environment or in a chemical medium with strong acid or alkali, titanium can maintain a stable structure and surface integrity for a long time. This unique advantage makes titanium the preferred material in aerospace, marine engineering, chemical equipment and other fields.
The corrosion resistance principle of titanium
The corrosion resistance of titanium comes from a dense, stable oxide film ( TiO ₂ ) that spontaneously forms on its surface. Although the standard electrode potential of titanium is –1.63 V, which is thermodynamically unstable, after exposure to air or water, its surface potential stabilizes at about +0.09 V (25°C seawater), forming a highly adherent and self-healing passivation film that effectively blocks oxygen, moisture, and corrosive ions.
of the oxide film is 1-2.5, which ensures that it can completely cover the metal surface and is not easy to crack. The film thickness can grow naturally from the initial 1.2-1.6 nm to about 9 nm (545 days), and can also be thickened by anodizing and other methods . Therefore , the oxide film generated by anodizing and thermal oxidation will significantly improve the corrosion resistance of titanium.
Corrosion resistance of titanium in different media
Inorganic acid
Titanium has excellent corrosion resistance in most oxidizing inorganic acids, especially in media such as nitric acid, chromic acid, hypochlorous acid, and perchloric acid. This is due to the stability of its surface passivation film, which can self-heal and maintain corrosion resistance even at high temperatures. Taking nitric acid as an example, titanium has no signs of corrosion in long-term use in nitric acid at a concentration of 60% at up to 193°C, making it an ideal metal material in nitric acid systems.
In contrast, in reducing acids such as sulfuric acid, hydrochloric acid and phosphoric acid, the corrosion resistance of pure titanium is relatively poor, the passivation film is easily destroyed, and the corrosion rate increases significantly with the increase of temperature and acid concentration. For example:
- Of less than 5% in sulfuric acid at room temperature with air flowing through it .
- To hydrochloric acid below 7% at room temperature ;
- The corrosion resistance to phosphoric acid decreases with increasing temperature, and it can only withstand concentrations below 2% at 100°C.
However, adding heavy metal ions (such as Fe, Ni, Cu, Mo) or alloying (such as titanium-palladium alloy, titanium-nickel-aluminum alloy) can significantly improve its corrosion resistance in reducing acids. For example, titanium-palladium alloy can withstand up to 27% hydrochloric acid solution at room temperature.
Therefore, when titanium equipment is used in an inorganic acid environment, the oxidizing property, temperature, concentration of the acid and whether corrosion inhibitors can be introduced or alloy strengthening can be used should be comprehensively considered to ensure service life and stability.
Organic acids and organic compounds
Titanium exhibits excellent corrosion resistance in most organic compounds, which is mainly due to its stable passivation film on the surface. Titanium's corrosion resistance to organic acids is closely related to the redox property of the medium, and is usually stable under oxidizing or air-permeable conditions. Only a few highly reducing media, such as hot formic acid, hot oxalic acid and concentrated trichloroacetic acid without air, may cause corrosion to titanium, but once oxygen is introduced, the corrosion rate will be significantly reduced.
The moisture and air in the organic medium help maintain the passive state of titanium. On the contrary, under high temperature and anhydrous conditions, organic matter may decompose and release hydrogen, causing titanium to absorb hydrogen and induce hydrogen embrittlement. Therefore, although titanium is less corrosive in such environments, its sensitivity to hydrogen embrittlement and stress corrosion should still be noted when used, especially in high temperature or closed systems.
In practical applications, titanium can stably withstand a variety of organic acids, such as acetic acid, citric acid, tartaric acid, lactic acid, etc., and has been successfully used in terephthalic acid and adipic acid media at 204°C and 67% concentration, fully demonstrating its reliability and durability in organic chemical and corrosive environments.
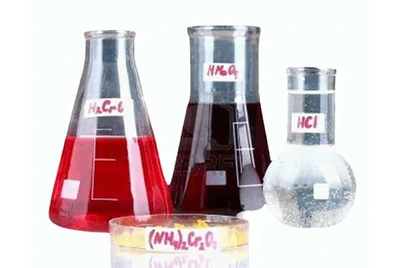
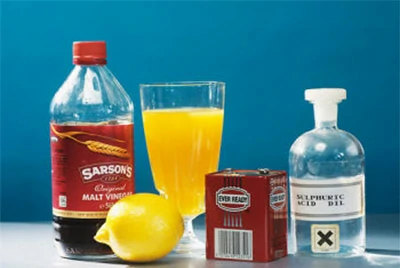
Alkaline medium
Titanium exhibits very strong corrosion resistance in alkaline media. Whether it is sodium hydroxide, potassium hydroxide, or common alkaline solutions such as ammonia, calcium hydroxide, and magnesium hydroxide, titanium can be used stably for a long time. In a boiling state, even in saturated calcium hydroxide, magnesium hydroxide, or ammonia, the corrosion rate of titanium is almost zero, showing extremely high corrosion resistance.
Even under harsh conditions, such as in a sodium hydroxide solution at 188°C and a concentration of 50% to 73%, the corrosion rate of titanium usually does not exceed 1.09 mm/a, which is still a very slow corrosion. However, in this high temperature and high alkaline environment, special attention should be paid to the problem of hydrogen embrittlement. Studies have shown that when the solution temperature exceeds 77°C and the pH value is higher than 12, titanium may absorb hydrogen, causing hydrogen embrittlement of the material, thereby affecting structural safety.
Therefore, although titanium has excellent overall corrosion resistance in alkaline environments, when used under high temperature and high alkaline conditions, the risk of hydrogen embrittlement still needs to be comprehensively considered to ensure the long-term reliability of the equipment.
Chlorine, chlorides and chlorine-containing compounds
Titanium has excellent corrosion resistance in wet chlorine gas, chloride solutions and most chlorine-containing compounds. In media such as chlorate, hypochlorite, chlorite and perchlorate, titanium can maintain a stable passivation film and is widely used in bleaching plants, electrolytic chlorine equipment and wastewater treatment systems, showing good long-term stability.
However, in high-temperature and high-concentration chloride solutions, such as ZnCl₂ , AlCl₃ and CaCl₂ , titanium may suffer from crevice corrosion, especially when it comes into contact with materials such as polytetrafluoroethylene and forms narrow crevice. Therefore, crevice formation should be avoided in structural design to reduce the risk of corrosion.
Titanium is very unstable in dry chlorine and can react violently with chlorine to form TiCl₄ , releasing a large amount of heat and even causing fire or spontaneous combustion. Only when there is enough water in the chlorine will TiCl₄ hydrolyze into stable titanium hydroxide, inhibiting the combustion of titanium.
Research shows that the minimum moisture content required for industrial pure titanium to maintain a passive state in a chlorine environment at 200°C is about 1.5%, while at room temperature, only 0.3% to 0.4% moisture is required to avoid spontaneous combustion. Titanium-palladium alloys and titanium-nickel-aluminum alloys are more stable under low humidity conditions and are suitable for more demanding chlorine-containing environments.
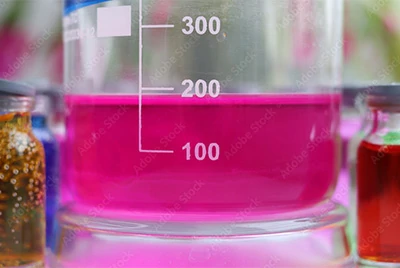
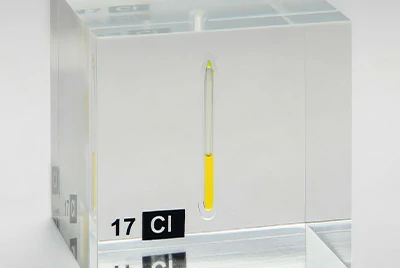
Bromine, iodine and fluorine and their compounds
The corrosion resistance of titanium in bromine and iodine environments is similar to that of chlorine. As long as there is a certain amount of moisture in the medium, the titanium surface can maintain a stable passivation film to avoid corrosion. Therefore, titanium can usually be used safely in conditions of wet bromine gas or iodine compounds.
In contrast, titanium does not have good corrosion resistance in fluorine and its compounds. Especially in hydrofluoric acid or acidic fluoride solutions, titanium will be corroded rapidly even in low concentrations. There are currently almost no effective corrosion inhibitors to prevent this process, so titanium is not suitable for use in fluorine-containing atmospheres or hydrofluoric acid-related environments.
However, if fluoride forms a complex with metal ions or is a structurally stable fluorocarbon, these special forms of fluoride generally do not corrode titanium, with certain exceptions. This should be judged based on the specific medium composition in the design application.
Corrosion resistance of titanium in river water and sea water
Titanium has extremely strong corrosion resistance in river water and seawater, especially in seawater environment, its corrosion resistance is about 100 times that of stainless steel, and it is one of the most corrosion-resistant metal materials in natural water. Even in high-temperature seawater up to 260°C, titanium can still work stably. In actual applications, for example, titanium tube condensers have been used in polluted seawater for more than 20 years, and the surface has only slightly changed color without obvious corrosion.
Titanium has good resistance to pitting, crevice and impact corrosion in seawater, and is also insensitive to stress corrosion and corrosion fatigue. In high-speed seawater (such as 36.6 m/s), the scouring effect is slightly enhanced, but it is still better than copper alloys and aluminum alloys.
When there are particles such as sand in seawater, the erosion of titanium will have a certain impact, but the overall damage is relatively light. Titanium also has excellent resistance to cavitation corrosion in seawater and is suitable for harsh marine conditions.
It should be noted that the surface of titanium materials is non-toxic and non-corrosive, and it can easily become a substrate for the attachment of marine organisms, which may lead to problems such as biofouling, and is a key factor to be considered in marine applications.
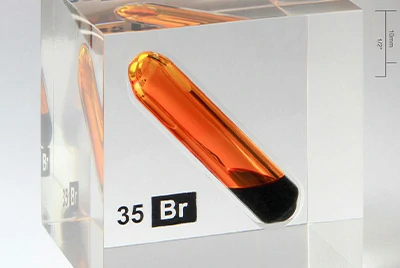
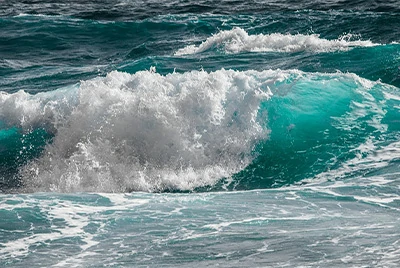
Corrosion rate of titanium in different media
The corrosion rate of industrial pure titanium depends not only on the type, concentration and temperature of the medium, but also on the state of the medium, such as whether it is ventilated, whether oxidizing or reducing compounds are added, etc.
Reagent | Concentration (%) | Temperature | Corrosion Rate (mm/a) | Evaluation |
---|---|---|---|---|
Hydrochloric acid | 1 | Room temp | 0 | Excellent |
Hydrochloric acid | 1 | Boiling | 0.345 | Good |
Hydrochloric acid | 5 | Room temp | 0 | Excellent |
Hydrochloric acid | 5 | Boiling | 6.53 | Poor |
Hydrochloric acid | 10 | Room temp | 0.175 | Good |
Hydrochloric acid | 10 | Boiling | 40.87 | Poor |
Hydrochloric acid | 20 | Room temp | 1.34 | Poor |
Hydrochloric acid | 35 | Room temp | 6.66 | Poor |
HCl + HNO₃ | 1:3 | Room temp | <0.127 | Excellent |
HCl + HNO₃ | 2:1 | Room temp | <0.127 | Excellent |
HCl + HNO₃ | 3:1 | Room temp | <0.127 | Excellent |
HCl + HNO₃ | 4:1 | Room temp | <0.127 | Excellent |
HCl + HNO₃ | 7:1 | Room temp | <0.127 | Excellent |
HCl + HNO₃ | 20:1 | Room temp | <0.127 | Excellent |
Sulfuric acid | 5 | Room temp | 0 | Excellent |
Sulfuric acid | 5 | Boiling | 13.01 | Poor |
Sulfuric acid | 10 | Room temp | 0.23 | Good |
Sulfuric acid | 60 | Room temp | 0.277 | Good |
Sulfuric acid | 80 | Room temp | 32.66 | Poor |
Sulfuric acid | 95 | Room temp | 1.4 | Poor |
Nitric acid | 37 | Room temp | 0 | Excellent |
Nitric acid | 37 | Boiling | <0.127 | Excellent |
Nitric acid | 64 | Room temp | 0 | Excellent |
Nitric acid | 64 | Boiling | 0.437 | Good |
H₂SO₄ + HNO₃ | 10:90 | Room temp | <0.127 | Excellent |
H₂SO₄ + HNO₃ | 30:70 | Room temp | <0.127 | Excellent |
H₂SO₄ + HNO₃ | 50:50 | Room temp | <0.127 | Excellent |
H₂SO₄ + HNO₃ | 60:60 | Room temp | <0.127 | Excellent |
Aqua regia (HNO₃:HCl) | 1:3 | Room temp | 0.004 | Excellent |
Aqua regia (HNO₃:HCl) | 1:3 | Boiling | <0.127 | Excellent |
Phosphoric acid | 10 | Room temp | 0 | Excellent |
Phosphoric acid | 10 | Boiling | 6.4 | Poor |
Phosphoric acid | 30 | Room temp | — | Excellent |
Phosphoric acid | 30 | Boiling | 17.6 | Poor |
Phosphoric acid | 50 | Room temp | 0.097 | Excellent |
Oxalic acid | 5 | Room temp | 0.127 | Excellent |
Oxalic acid | 5 | Boiling | 29.39 | Poor |
Acetic acid | 0 | Room temp | 0.008 | Excellent |
Acetic acid | 100 | Room temp | — | Excellent |
Acetic acid | 100 | Boiling | — | Excellent |
Formic acid | 50 | Room temp | 0 | Excellent |
Chromic acid | 20 | Room temp | <0.127 | Excellent |
Chromic acid | 20 | Boiling | <0.127 | Excellent |
Lactic acid | 10 | Room temp | — | Excellent |
Lactic acid | 10 | Boiling | 0.033 | Excellent |
Tannic acid | 25 | Room temp | <0.127 | Excellent |
Tannic acid | 25 | Boiling | <0.127 | Excellent |
Citric acid | 50 | Room temp | <0.127 | Excellent |
Citric acid | 50 | Boiling | 0.127–1.27 | Good |
Stearic acid | — | Room temp | <0.127 | Excellent |
Stearic acid | — | Boiling | <0.127 | Excellent |
Sodium hydroxide | 20 | Room temp | — | Excellent |
Sodium hydroxide | 20 | Boiling | <0.127 | Excellent |
Sodium carbonate | 20 | Room temp | <0.127 | Excellent |
Sodium carbonate | 20 | Boiling | <0.127 | Excellent |
Sodium chloride | Saturated | Room temp | <0.127 | Excellent |
Sodium chloride | Saturated | Boiling | <0.127 | Excellent |
Ammonium chloride | 10 | Room temp | <0.127 | Excellent |
Ammonium chloride | 10 | Boiling | 0 | Excellent |
Magnesium chloride | 10 | Room temp | <0.127 | Excellent |
Magnesium chloride | 10 | Boiling | <0.127 | Excellent |
Ammonia (aqueous) | 10 | Room temp | <0.127 | Excellent |
Ammonia (aqueous) | 10 | Boiling | <0.127 | Excellent |
Hydrogen peroxide | 5 | Room temp | <0.051 | Excellent |
Hydrogen peroxide | 5 | Boiling | <0.127 | Excellent |
Types of corrosion of titanium
Titanium has a strong corrosion resistance in a variety of corrosive environments due to its stable passivation film. However, corrosion failure may still occur under specific media, structural conditions or stress. According to the scope and form of corrosion, titanium corrosion can be divided into two categories: general corrosion and local corrosion.
General corrosion
General corrosion refers to the phenomenon that titanium dissolves uniformly on the surface in a corrosive medium. It usually occurs in a strong reducing environment where the passive film cannot be formed or is destroyed, such as high-temperature concentrated hydrochloric acid or hydrofluoric acid. This type of corrosion is predictable and easy to control, and the impact on equipment life can be managed through wall thickness design and regular maintenance. In most neutral or weakly corrosive media, titanium hardly undergoes general corrosion, so it is widely used in chemical, marine and medical fields. .
Localized corrosion
Compared with general corrosion, local corrosion is more destructive and often occurs and expands rapidly in local areas, which can easily cause equipment perforation, failure or sudden fracture. Local corrosion of titanium mainly includes the following typical types:
Crevice corrosion is the corrosion of titanium in structural gaps or stagnant areas of the medium, which is common in flange connections, gasket seals or under sediments. Due to the limited oxygen transmission, the local passive film fails and forms a corrosion cell, which leads to acidification and increased corrosion in the crevice area. Although titanium is stable in most seawater and industrial water, crevice corrosion may occur if chloride ions accumulate in the crevice.
Pitting corrosion is characterized by local perforation corrosion, which often occurs in the presence of halogen ions such as Cl⁻ , Br⁻ , and F⁻ . These ions have a destructive effect on the passivation film, causing corrosion to be concentrated in a small area and penetrate rapidly, forming corrosion pits that are difficult to detect with the naked eye but highly destructive. Titanium needs to be particularly vigilant against this type of corrosion in environments such as static seawater and chloride solutions.
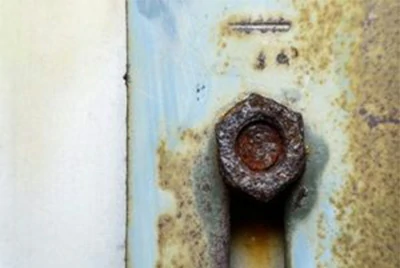
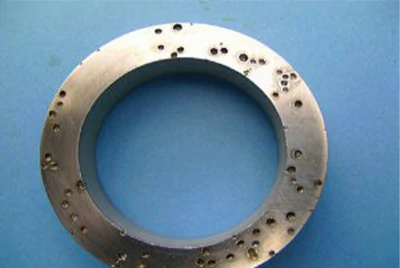
Stress corrosion cracking is a form of cracking and brittle fracture caused by the combined action of corrosive media and tensile stress. Although titanium is not prone to such cracking in most media, some titanium alloys may be susceptible to stress corrosion in high-temperature environments containing chloride or in the presence of residual stress.
Abrasive corrosion is a corrosion phenomenon caused by the combined effects of mechanical erosion and electrochemical corrosion. In high-speed flowing sandy water or seawater cooling systems, the surface passivation film of titanium may be periodically destroyed due to erosion, resulting in local metal exposure and accelerated corrosion. This should be paid special attention to in heat exchangers, condensers and piping systems.
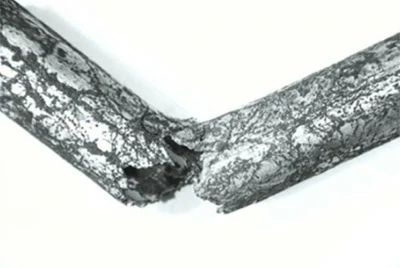
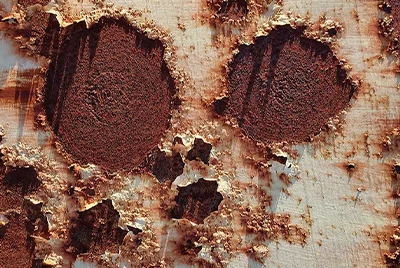
Galvanic corrosion occurs when titanium is in direct contact with other metal materials and there is a conductive medium. Since titanium has a high electrode potential, when it is connected to metals such as carbon steel and stainless steel, the metal with a lower potential will become the anode and dissolve first, causing accelerated corrosion. Therefore, when designing a mixed structure of titanium and dissimilar metals, direct contact should be avoided or isolation and cathodic protection measures should be taken.
Hydrogen absorption and hydrogen embrittlement are also possible failure mechanisms of titanium materials under certain conditions. Titanium easily absorbs hydrogen atoms and forms hydrides in the presence of active hydrogen sources such as high-temperature alkali solutions or acidic fluorides. When hydrogen exceeds its solid solubility limit, titanium loses its toughness and cracks, which can lead to material fracture or failure in severe cases.

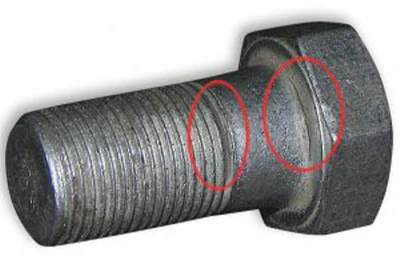
Comparison of corrosion resistance between titanium and aluminum
Compare projects | Titanium | Aluminum |
---|---|---|
Passivation film composition | Titanium dioxide (TiO ₂ ) | Alumina ( Al₂O₃ ) |
Oxide film thickness (room temperature, nanometers) | 1.2 – 1.6 | twenty three |
Repassivation speed | Very fast (within seconds) | Medium speed |
Corrosion rate in 3.5% sodium chloride (mm/a) | <0.005 | 0.1 – 1.0 |
Corrosion resistance to 60% nitric acid | Excellent, long-term stability | Very poor, easy to dissolve quickly |
Corrosion resistance to 20% boiling sodium hydroxide | <0.127 | Rapid corrosion |
Resistance to seawater crevice corrosion | Very strong | Poor, easy to pitting |
Stress Corrosion Cracking Susceptibility | Low sensitivity | Moderate to high sensitivity |
Pitting potential in NaCl (V vs SCE) | >1.2 | <0.2 |
Operating temperature range (°C) | -250 to 400 | -80 to 150 |
Typical service life in seawater | >20 years | 3–5 years (depending on alloy) |
Marine environment suitability | Very suitable for | limited |
Typical applications of titanium in highly corrosive industries
Chlor-alkali and acid industry
In chlor-alkali, electrolysis and acid-making systems, titanium can resist strong corrosive media such as high-concentration chloride ions, nitric acid and hydrochloric acid, and is widely used in electrolytic cells, heat exchangers, acid circulation pipelines and other equipment. Compared with traditional metals, titanium materials have higher stability, longer life and lower maintenance costs in these environments.
Seawater desalination and marine engineering
Titanium is highly resistant to chlorides, sand erosion and marine organism attachment in seawater, and is an ideal material for desalination equipment, condensers, pumps and valves, and marine structures. In high-velocity and high-salinity environments, titanium hardly suffers from pitting or crevice corrosion, ensuring long-term reliable operation of the equipment.
Nuclear energy
In nuclear power systems, titanium can withstand high temperatures, high pressures and corrosive coolants, and has good radiation resistance. It is often used in nuclear-grade heat exchange tubes, structural support parts and piping systems to ensure the safe and stable operation of equipment under harsh working conditions.
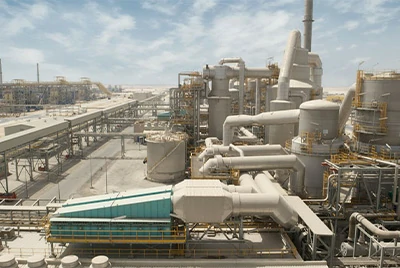
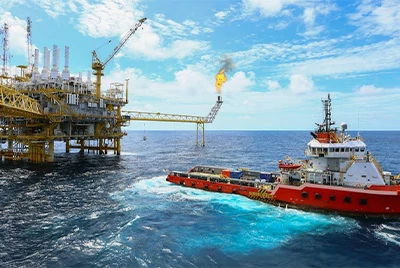
What corrosion protection services does Chalco offer for titanium products?
Alloy strengthening
Chalco improves the corrosion resistance of titanium by alloying. After adding elements such as palladium, nickel, and molybdenum, the stability of titanium in reducing acid and high chloride environments is significantly improved. For example, titanium-palladium alloy has excellent performance in hydrochloric acid and sulfuric acid media and is widely used in chemical industry, metallurgy, seawater treatment and other fields.
Environmental Control
In certain working conditions, Chalco can provide recommendations for the use of corrosion inhibitors to stabilize the passive film on the titanium surface and reduce the corrosion rate by adjusting the medium composition. This strategy is suitable for cooling water systems, closed-loop process flows, and other scenarios where it is inconvenient to replace materials.
Precious metal surface treatment
For systems with strong electrochemical environments or high corrosion risks, Chalco can provide precious metal surface treatment solutions. By depositing precious metals such as platinum or palladium on the titanium surface, the stability and regeneration ability of the passivation film can be further improved, which is widely used in chlor-alkali, electrolysis, and marine systems.
Thermal oxidation treatment
Chalco can perform thermal oxidation treatment on titanium materials to form a thick and dense oxide film on their surface, enhancing their corrosion resistance in high temperature, water vapor and acidic gas phases. It is suitable for high temperature and high corrosion occasions such as towers and heat exchange equipment.
Anodic protection
In continuously running equipment or large titanium structures, Chalco can assist customers in establishing an anodic protection system to keep titanium at a passive potential through impressed current, thereby effectively delaying corrosion. This method is suitable for the protection of key parts in industries such as petrochemicals, electrolysis, and water treatment.