Titanium Melting Point Guide
Updated : Jul. 9, 2025The titanium melting point is a key factor in aerospace, medical, and industrial applications.
Many buyers and engineers focus on its strength and corrosion resistance—but often overlook how a high melting point affects casting, welding, and processing costs.
Understanding titanium's melting point helps you choose the right material, optimize production, and reduce risks.
What is the melting point of titanium?
The titanium melting point is around 1,725°C (3,135°F). This exceptionally high temperature reflects its strong metallic bonds and explains why titanium remains stable under extreme heat.
Understanding how different titanium grades melt helps engineers and buyers make better material choices.
Here's a quick reference table of titanium and alloy melting points:
Material | Melting Point (°C) | Melting Point (°F) | Notes |
---|---|---|---|
Pure Titanium (Grade 1–4) | 1,668 | 3,034 | Grades 1–4: higher strength comes with lower ductility |
Ti-6Al-4V (Grade 5) | 1,655 | 3,011 | Most used alloy; great strength and weldability |
Ti-6Al-4V ELI (Grade 23) | 1,655 | 3,011 | Preferred for medical implants |
Ti-3Al-2.5V (Grade 9) | 1,650 | 3,002 | Easy to form; ideal for titanium tubing |
Ti-5Al-2.5Sn | 1,645 | 2,993 | Alpha alloy with good high-temp stability |
Ti-10V-2Fe-3Al | 1,675 | 3,047 | Beta alloy; high strength and good hardenability |
Ti-6Al-2Sn-4Zr-2Mo (Ti 6242) | 1,650 | 3,002 | Alpha-beta alloy; excellent high-temp performance |
Ti-6Al-2Sn-4Zr-6Mo (Ti 6246) | 1,660 | 3,020 | Stronger beta stability; used in high-stress parts |
Ti-15V-3Cr-3Sn-3Al | 1,660 | 3,020 | Superplastic alloy; good for forming complex shapes |
Ti-8Al-1Mo-1V | 1,650 | 3,002 | Great resistance to high-temp creep |
Why is the titanium melting point so high?
Titanium melts at 1,725°C (3,135°F)—much higher than most common metals. Several factors contribute to this:
Strong metallic bonding
Titanium atoms form tight metallic bonds by sharing electrons in a "sea of electrons.” These bonds require high temperatures to break.
Dense crystal structure
Titanium has a hexagonal close-packed (hcp) structure at room temperature, shifting to body-centered cubic (bcc) at high heat. Both are tightly packed, boosting stability and melting point.
High lattice energy
Strong atomic attraction creates a stable lattice. More energy is needed to overcome this and melt the metal.
Unique electron configuration
Titanium's d-electrons strengthen atomic bonding, making the structure harder to break apart.
Alloying effects
Adding elements can stabilize the atomic structure, sometimes raising the melting point further.
While titanium itself melts at a high temperature, real-world applications may show variation depending on alloying and processing conditions.
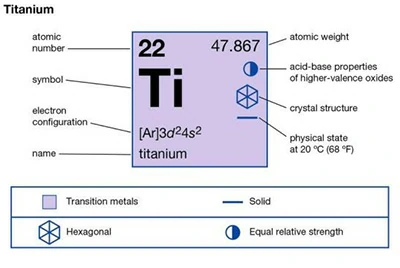
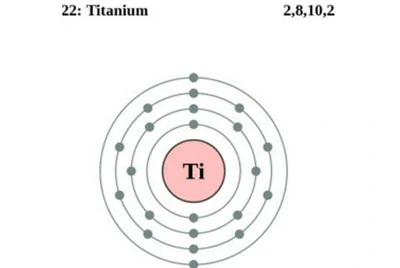
Does the titanium melting point change?
Standard titanium melts at about 1,668 °C (3,034 °F), yet this number isn't fixed in the field.
Several factors can shift the titanium melting point:
Purity
- Higher purity keeps the melting point close to the textbook figure.
- Impurities such as oxygen, nitrogen, or carbon weaken metallic bonds and lower the melting point.
- Industrial titanium often carries trace impurities, so its melting point sits slightly lower.
Alloying elements
- Titanium is routinely alloyed; each added metal nudges the melting range.
- Ti-6Al-4V, for example, melts around 1,655 °C, just below pure titanium.
- Aluminum, vanadium, tin, and molybdenum all influence where melting starts.
Microstructure and phase composition
- Titanium switches between dense α-phase (hcp) and high-temperature β-phase (bcc).
- α is stable at lower heat; β forms at high heat and can be stabilized with vanadium.
- These phase shifts dictate how—and when—an alloy begins to melt.
Pressure
Under high pressure, the titanium melting point increases. The greater the pressure, the harder it is for atoms to shift from solid to liquid—making the metal more resistant to melting.
Heating atmosphere
The surrounding environment during heating also matters.
In oxygen- or nitrogen-rich conditions, titanium can form surface layers of titanium oxide or nitride.
These compounds alter how titanium melts and impact thermal behavior.
How to raise titanium's melting point
The titanium melting point can be raised by improving purity, refining crystal structure, adding high-melting-point alloying elements, and using advanced melting techniques—enhancing its stability and performance in high-temperature environments.
Titanium's high melting point empowers high-temperature applications
With a melting point of 1,668°C (3,034°F), titanium outperforms stainless steel, aluminum, and many common metals.
Combined with its high strength, low density, corrosion resistance, and biocompatibility, titanium excels in extreme and high-heat environments.
Aerospace
Titanium retains its strength and structural integrity at high temperatures, making it ideal for critical aerospace components.
- Turbine blades and engine casings
- Landing gear and structural frames
- Heat shields and fasteners
Automotive
Lightweight and strong, titanium helps boost performance and reduce weight in high-end vehicles.
- Exhaust systems and suspension links
- Valve assemblies and wheel hubs
- Engine internals
Chemical processing & industrial equipment
Titanium's corrosion resistance and high melting point allow it to withstand high heat, pressure, and aggressive chemicals.
- Heat exchangers and reactors
- High-temperature piping, pumps, and valves
- Storage tanks for corrosive media
Marine engineering
Titanium resists seawater corrosion, making it reliable for deep-sea, high-pressure, and high-temperature conditions.
- Propeller shafts and seawater intake systems
- Submarine frames and offshore platform parts
- Marine heat exchangers and fasteners
Manufacturing and tooling
Titanium is ideal for high-temperature molds, fixtures, and cutting tools.
It maintains dimensional accuracy in demanding processes like die casting and injection molding.
- Heat-resistant molds and jigs
- Thermal-stable cutting tools and clamps
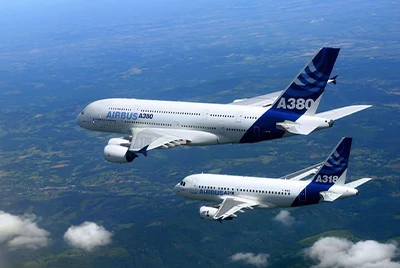
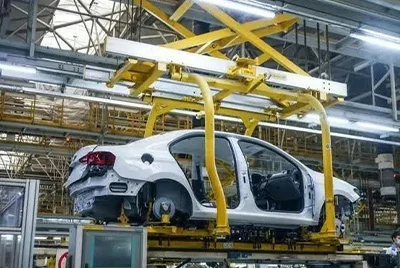
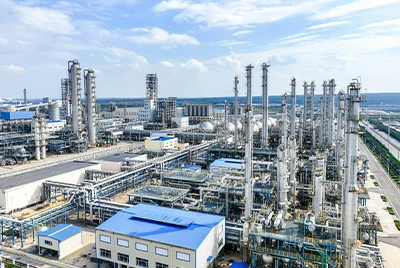
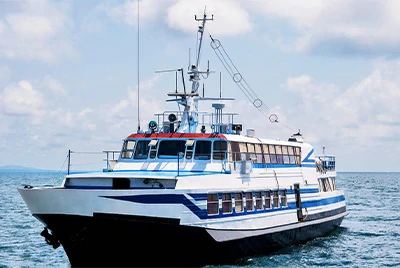
Processing challenges of titanium's high melting point
Melting is energy-intensive
Titanium must be melted using high-temperature systems like vacuum arc remelting (VAR).
Maintaining such heat demands massive energy and raises operating costs.
Strict welding requirements
At high temperatures, titanium absorbs oxygen and nitrogen easily, leading to contamination.
Welding must be done under high-purity inert gas, such as argon.
It also demands tighter control over weld seams and gas shielding.
Machining is difficult
Titanium work hardens quickly and wears out tools fast.
It requires special tooling, low cutting speeds, and high feed rates.
Casting is complex
Standard casting methods struggle with titanium's high melting point.
Graphite or ceramic molds in a high-vacuum environment are often used.
Improper temperature control can cause shrinkage, cracking, or oxide inclusions.
Additive manufacturing requires more power
3D printing titanium powder with lasers or electron beams needs high energy density.
This pushes equipment to its limits and requires precise scanning and fusion control.
Despite the difficulty and cost, high-performance titanium parts can be produced reliably—
as long as you apply the right parameters, advanced equipment, and strict quality control.
The key is to strike the perfect balance between safety, efficiency, and product integrity.
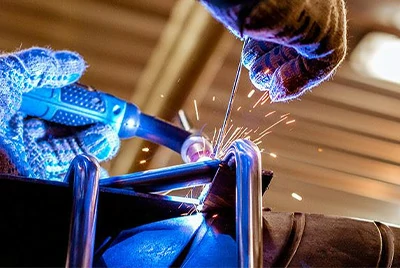
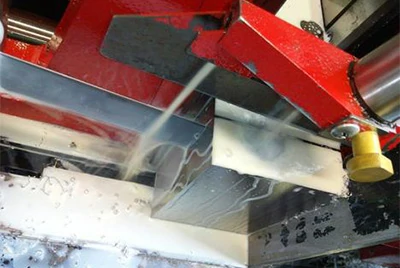
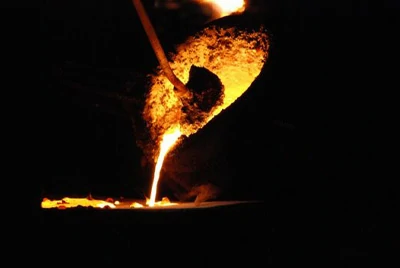
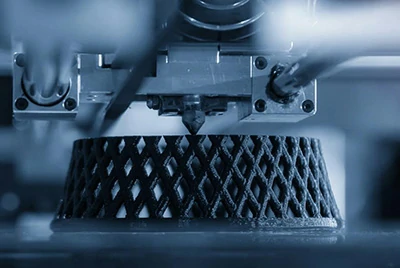
Melting point comparison: titanium vs. common metals
As shown below, the titanium melting point is significantly higher than most common metals:
Metal Element | Melting Point (°C) | Notes |
---|---|---|
Lead (Pb) | 327.5 | Soft, non-structural metal; common in low-temp applications |
Aluminum (Al) | 660 | Lightweight metal with high thermal conductivity |
Brass | 930–1000 | Copper-zinc alloy; varies by composition |
Copper (Cu) | 1,084 | Excellent conductivity; widely used in electrical systems |
Nickel (Ni) | 1,455 | Corrosion-resistant; common in alloys and chemical equipment |
Steel | 1,370–1,540 | Range depends on carbon content and alloying elements |
Cobalt (Co) | 1,495 | Magnetic alloy element for high-temp uses |
Thorium (Th) | 1,755 | Radioactive metal |
Vanadium (V) | 1,910 | Alloying element to boost strength |
Iridium (Ir) | 2,446 | Extremely dense and corrosion-resistant |
Rhodium (Rh) | 1,963 | Precious metal, used in catalytic converters |
Tantalum (Ta) | 3,020 | High-melting metal for corrosive environments |
Tungsten (W) | 3,422 | Highest melting point of all metals |
FAQ: titanium melting point and high-temperature questions
What can melt titanium?
Titanium melts at 1,725°C (3,135°F). Melting typically requires high-temperature heat sources like electric arc furnaces, induction furnaces, or plasma arc welding systems.
Why is titanium so expensive?
Titanium is costly due to its energy-intensive extraction process (the Kroll method), high melting point, and complex machining requirements. These factors make it far more expensive than common metals.
Can titanium be melted and reused?
Yes. Titanium scrap can be remelted and recycled using arc or induction melting, especially in high-value industries like aerospace and medical.
Why is titanium better than stainless steel in high-heat environments?
Titanium retains high strength at elevated temperatures and resists oxidation better than stainless steel. It performs especially well above 600°C, where stainless steel tends to weaken.
Would titanium melt in lava?
No. Lava typically reaches 1,100–1,200°C, well below titanium's melting point of 1,660–1,725°C. Titanium remains solid in molten lava.
How long does it take to melt titanium?
In lab settings, with a 5 kW heat source, titanium can reach its melting point in about 60 seconds. In industrial scenarios, melting time varies depending on volume, furnace type, and heating efficiency.
Chalco Titanium is committed to delivering one-stop titanium alloy solutions to global clients—covering everything from raw material supply to custom processing.
We serve a wide range of industries including aerospace, chemical, medical, energy, and automotive.
Chalco can provide you the most comprehensive inventory of titanium products and can also supply you customized products. Precise quotation will be provided within 24 hours.
Get a quote