Titanium vs Stainless Steel
Updated : Jun. 23, 2025When selecting suitable metal materials for a project, titanium and stainless steel are often the two major options compared. Both materials offer excellent mechanical properties and corrosion resistance, but they differ significantly in weight, strength-to-weight ratio, cost, and application areas.
We will comprehensively compare titanium and stainless steel across several key dimensions to help you make a more informed material choice based on specific project requirements, industry environment, and budget.
What is titanium?
Titanium, with the chemical symbol Ti, is a low-density silver-white transition metal known for its light weight, high strength, and corrosion resistance.
It is widely used in aerospace, medical implants, and high-performance engineering fields, commonly shaped by forging, machining, or casting. Titanium materials are divided into commercially pure titanium and titanium alloys, customized to meet different application needs.
What is stainless steel?
Stainless steel is an alloy steel primarily composed of iron, chromium (10–30%), and other elements such as nickel, molybdenum, and titanium, offering excellent corrosion resistance and high-temperature performance.
By adjusting the alloy composition, stainless steel can achieve a balance of strength, corrosion resistance, and machinability in various industrial environments.
Physical properties of titanium and stainless steel
Density
Density is one of titanium’s greatest advantages due to its extremely low value. Titanium has a density of about 4.5 g/cm³, while most stainless steels, such as 304 or 316, have densities ranging between 7.75 and 8.1 g/cm³. This means that for the same volume, titanium weighs roughly half as much as stainless steel.
Thermal conductivity
Thermal conductivity is an area where stainless steel generally outperforms titanium. Titanium has a thermal conductivity of about 21.9 W/m·K, while stainless steel’s thermal conductivity varies depending on the grade, usually ranging between 15 and 25 W/m·K.
Melting point
Titanium has a higher melting point of about 1668°C (3034°F), which is significantly higher than stainless steel’s melting point of 1370–1450°C (around 2500°F).
This gives titanium greater structural stability in high-temperature environments, making it less prone to softening or strength loss. It is especially suitable for use in aerospace engines, high-temperature chemical reaction equipment, exhaust systems, and other extreme heat conditions.
Magnetism
Titanium is a completely non-magnetic metal, which is critically important in applications where magnetic interference must be avoided, such as medical imaging equipment (MRI), avionics, or high-precision instruments.
The magnetism of stainless steel depends on its specific type. Austenitic stainless steels like 304 and 316 are nearly non-magnetic, while ferritic or martensitic stainless steels, such as 430, possess a certain level of magnetism.
Chemical properties of titanium and stainless steel
Corrosion resistance
Titanium is well known for its excellent corrosion resistance. When exposed to air, it quickly forms a dense titanium oxide film that is nearly impenetrable and resists attack from most acids, salts, and chlorides. This makes titanium an ideal material for harsh environments such as marine, chemical, and outdoor applications.
Stainless steel performs well in normal environments, especially austenitic grades like 304 and 316. However, it is prone to pitting or stress corrosion in chloride-rich environments or crevices. To extend its service life, regular maintenance or protective coatings are often required to isolate it from air and moisture.
Chemical reactivity
Titanium has a high affinity for oxygen and rapidly reacts with it to form a protective oxide layer when exposed to air or high temperatures. This reactivity enhances corrosion resistance but also requires inert gas protection during welding or heat treatment to avoid contamination or embrittlement.
Stainless steel has relatively low chemical reactivity and can remain stable in various acidic and alkaline environments. By adjusting the alloy composition—such as adding molybdenum, titanium, or copper—its stability and corrosion resistance in specific chemical media can be improved to meet broader industrial needs.
Oxidation resistance
Titanium maintains the stability of its oxide film even at high temperatures. This film has excellent thermal stability and is not easily flaked off, allowing titanium to remain stable over time in environments with thermal corrosion or high humidity. It is especially suitable for high-temperature corrosion or thermal reaction equipment.
Stainless steel also offers good oxidation resistance and can maintain its surface integrity in medium to high temperatures. However, long-term exposure to high heat, oxygen, or humid environments may cause discoloration or scaling. Choosing heat-resistant stainless steel, such as 310S, can improve this condition.
Mechanical properties of titanium and stainless steel
Properties | Titanium | Stainless Steel |
---|---|---|
Tensile Strength | 900-1,200 MPa (130-174 ksi) | 480-1,100 MPa (70-160 ksi) |
Yield Strength | 800-1,100 MPa (116-160 ksi) | 240-800 MPa (35-116 ksi) |
Vickers Hardness | 180-400 HV | 150-300 HV |
Brinell Hardness | 250-350 HB | 150-400 HB |
Rockwell Hardness | 30-40 HRC | 20-40 HRC |
Elongation | 10-30% | 30-50% |
Elastic Modulus | 110-120 GPa (16-17.4 Mpsi) | 200-210 GPa (29-30.5 Mpsi) |
Tensile strength
Titanium typically has a tensile strength of 900–1200 MPa, offering extremely high structural strength. It can withstand heavy loads without breaking, making it a common material in demanding industries such as aerospace and medical applications.
Stainless steel generally has a tensile strength of 480–1100 MPa. High grades like 316L and 904L can match titanium, but most standard stainless steels fall short, limiting their use in high-strength applications.
Yield strength
Titanium has a yield strength of 800–1100 MPa, providing strong resistance to deformation and maintaining structural stability under high stress. This makes it more reliable in conditions with continuous load variations.
Stainless steel has a yield strength range of 240–800 MPa, depending on the material grade. In high-load or long-term stress scenarios, its resistance to deformation is generally lower than that of titanium.
Hardness
Titanium usually has a Vickers hardness of 300–400 HV, offering good wear resistance. It effectively resists friction and surface scratches, making it suitable for components that require abrasion resistance.
Standard stainless steel has a hardness of about 150–300 HV, but some hardened types like 440C can exceed 700 HV. While titanium is generally more wear-resistant, certain stainless steels also perform well in extreme wear conditions.
Fatigue resistance
Titanium alloys exhibit excellent fatigue resistance and can endure long-term alternating loads. They maintain ductility even under high stress or in oxygen-deprived environments, making them ideal for structures subject to frequent vibrations or impacts.
Stainless steel has moderate fatigue resistance under normal conditions but tends to degrade in high-stress or corrosive environments. In comparison, titanium offers greater stability and reliability in terms of fatigue life.
Machinability comparison between titanium and stainless steel
Casting
Titanium is typically cast using vacuum melting or argon arc melting processes, with a melting point of approximately 1,660 °C (3,020 °F). Cast titanium offers good strength but may develop defects like porosity during the forming process.
Stainless steel is commonly cast using investment or sand casting, with a melting range of 1,370–1,540 °C (2,500–2,800 °F). Its cast parts generally feature smooth surfaces and uniform structures, delivering overall better casting quality than titanium.
Machining
Due to its high toughness and low thermal conductivity, titanium must be machined at low cutting speeds (20–40 m/min) and relatively high feed rates. It imposes high cutting forces and causes rapid tool wear.
Stainless steel offers better machinability, with cutting speeds up to 100 m/min depending on the grade. With appropriate parameters, it can achieve good surface finish and dimensional accuracy.
Plastic forming
Titanium is usually formed through hot working, with an optimal temperature range of 800–1,200 °C. Hot forming significantly improves its ductility and formability, making it suitable for medium- to high-temperature shaping.
Stainless steel can undergo both cold and hot forming, with hot working temperatures around 1,100–1,200 °C. It exhibits excellent ductility and maintains strength and dimensional stability after processing.
Welding
Titanium welding is typically done via gas tungsten arc welding (GTAW) in an inert gas environment to prevent oxidation at high temperatures. The resulting welds have high strength and excellent corrosion resistance, though the process is technically demanding.
Stainless steel is compatible with a variety of common welding techniques, including TIG and MIG. It has better overall weldability, strong joint integrity, and wide applicability in structural components.
Surface treatment
Common surface treatments for titanium include anodizing and sandblasting. Anodizing enhances corrosion resistance and creates various colors for improved aesthetics.
Stainless steel often undergoes passivation, polishing, or coating. These treatments boost corrosion resistance and surface finish, making it ideal for applications in food, medical, and architectural fields where appearance is important.
Applications of titanium and stainless steel
Both titanium and stainless steel are widely used across various industries, but their physical properties and chemical stability determine their suitability for different fields. Although both have good corrosion resistance, differences in strength, weight, machinability, and biocompatibility make each more suitable for specific applications.
Typical applications of titanium
The aerospace industry widely uses this material in aircraft structural components, rocket parts, and spacecraft, mainly because of its high strength-to-weight ratio and excellent corrosion resistance.
In medical devices, it is suitable for artificial joints, bone screws, prosthetics, and surgical instruments, benefiting from its superior biocompatibility and corrosion resistance.
In marine engineering, the material is applied in ship parts, underwater equipment, and offshore platforms, capable of withstanding long-term seawater corrosion.
In sports equipment, it is used to manufacture high-performance bicycles, golf clubs, and tennis rackets that have strict requirements for weight and strength.
In chemical equipment, it is commonly used for manufacturing acid- and alkali-resistant containers, reactors, heat exchangers, and process pipelines that operate under high temperature and corrosive conditions.
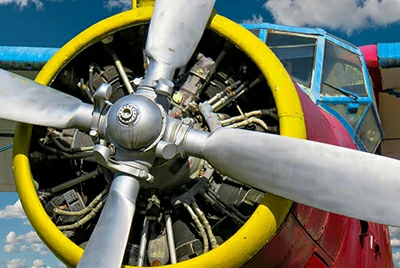
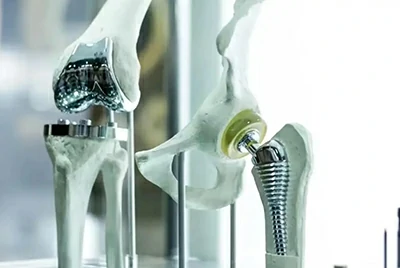
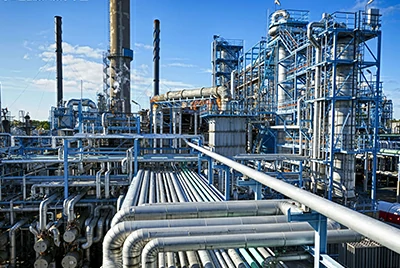
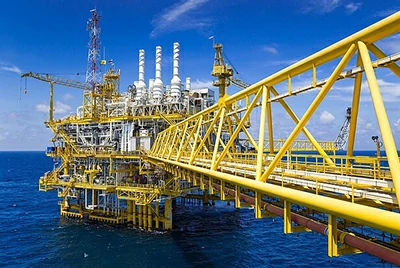
Typical applications of stainless steel
In the construction industry, this material is used for curtain walls, railings, structural components, and roofing systems, offering both structural strength and aesthetic appeal.
In automotive manufacturing, it is often used for exhaust pipes, engine parts, and chassis brackets due to its high-temperature resistance and corrosion resistance.
In kitchen and bathroom products, such as cookware, cutlery, and sinks, it is widely adopted because it is rust-resistant, easy to clean, and meets hygiene and safety standards.
In medical equipment, it is used for surgical instruments, diagnostic devices, and sterilization equipment, offering antibacterial, corrosion-resistant, and easy-to-clean properties.
In industrial equipment, including pumps, valves, storage tanks, and pipelines, it is extensively used to cope with various chemical media and high-temperature environments.
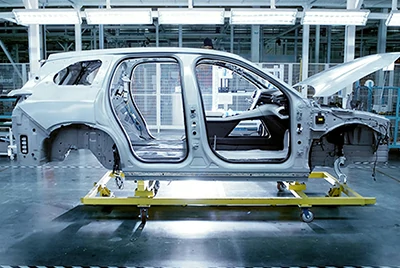
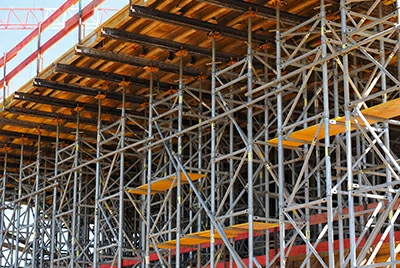
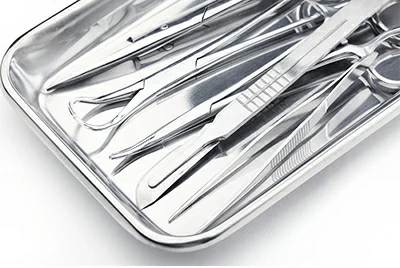
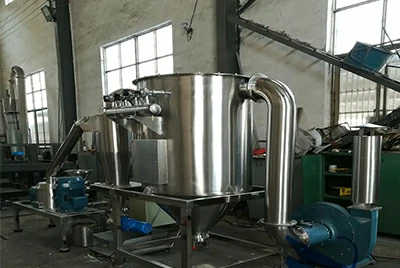
Price differences between titanium and stainless steel
Titanium is generally much more expensive than stainless steel, mainly due to the difficulty of raw material extraction, the complexity of the smelting process, and high processing costs. The price per unit weight of titanium is several times that of 304 stainless steel and can be even higher during special periods. Moreover, titanium requires higher standards for welding, cutting, and forming processes, and tool wear is significant, which further increases overall manufacturing costs.
In contrast, stainless steel (such as 304 and 316) has cheaper raw materials, a mature global supply chain, widely used processing techniques, and lower labor and energy costs, making it more cost-effective for most general industrial and commercial projects.
Advantages and disadvantages of titanium and stainless steel
Advantages of titanium
Titanium has extremely strong corrosion resistance. The naturally formed oxide film on its surface effectively resists corrosion from most acids, alkalis, and seawater.
Titanium is lightweight and high-strength. Its density is about 55% that of stainless steel, but it has comparable or even higher strength, making it ideal for lightweight structures.
Titanium has excellent thermal stability, with a melting point up to 1668°C, suitable for high-temperature equipment such as aircraft turbines.
It possesses excellent biocompatibility, is non-toxic and non-magnetic, which is why it is widely used in medical implants and surgical instruments.
Titanium has strong dimensional stability and will not expand or contract under high pressure and high temperature, ensuring structural stability.
Disadvantages of Titanium
Titanium is costly. Due to complex raw material extraction and processing, its procurement and manufacturing costs are far higher than stainless steel.
Processing is difficult. Titanium has high toughness and low thermal conductivity, requiring advanced equipment for cutting and welding, and longer processing times.
Titanium has a relatively low elastic modulus. Its resistance to deformation is somewhat weaker, so special design is needed for some high-load structures.
Advantages of stainless steel
Cost-effective, with lower raw material prices and wide availability, suitable for large-scale applications.
Good structural strength, providing mechanical strength and durability that maintain stability under extreme conditions such as storms and earthquakes.
Good corrosion resistance, especially austenitic stainless steels (like 304, 316) perform excellently in most industrial environments.
Strong sustainability, stainless steel is recyclable with a long service life and environmentally friendly.
High processing flexibility, easy to cut, weld, and form, suitable for customization and mass production.
Disadvantages of stainless steel
Requires maintenance for corrosion protection; prone to pitting in high-chloride or crevice environments, so regular upkeep or protective treatment is necessary.
Limited high-temperature performance; may deform under high heat, potentially affecting structural stability.
Limited appearance; untreated surfaces usually have moderate finish and lack decorative appeal.
How to choose between titanium and stainless steel in your project?
Titanium and stainless steel each have their advantages. When selecting materials, you should consider factors such as the project’s functional requirements, operating environment, budget constraints, and processing methods.
Projects suitable for choosing titanium
For weight-sensitive fields, such as aerospace components, medical implants, and high-performance sports equipment, titanium’s density is only about 55% that of stainless steel, significantly reducing weight.
For applications exposed long-term to corrosive environments, such as seawater pipelines, chemical containers, and offshore platforms, titanium offers excellent resistance to chlorides, salt spray, and acidic or alkaline media, requiring no additional corrosion protection.
For equipment requiring high-temperature strength and thermal stability, such as turbines, reactors, and exhaust systems, titanium’s melting point reaches 1668°C, making it resistant to softening or oxidation at elevated temperatures.
For cases demanding strict biocompatibility, such as artificial joints, dental implants, and surgical instruments, titanium is non-toxic, non-magnetic, and does not cause rejection reactions in the human body.
For structural parts that require long service life and low maintenance, such as deep-sea exploration devices and critical pressure vessels, titanium is ideal for situations where frequent repairs or replacements are not feasible.
Projects suitable for choosing stainless steel
When budgets are limited and cost control is important, such as building railings, pipe supports, or structural connectors, stainless steel is often the wiser choice. Compared to titanium, stainless steel materials and processing costs are lower, making it suitable for large-scale procurement.
For applications requiring high strength and wear resistance, such as automotive exhaust systems, pumps, valves, and kitchen hardware, stainless steel provides solid structural strength. Its durability is especially notable after hardening treatment.
In relatively mild environments, such as indoor installations, ambient temperature piping, or food processing equipment, grades like 304 and 316 stainless steel perform reliably and easily meet daily use requirements.
For parts needing quick delivery and flexible processing, such as components requiring rapid cutting, welding, or bending, stainless steel is the preferred option due to its mature manufacturing processes and good machinability.
If appearance is important, such as decorative panels, elevator interiors, or sinks, stainless steel can be polished or brushed to create a stylish and easy-to-maintain surface finish.