Weld Titanium
Updated : Jun. 25, 2025Introduction to titanium welding
Titanium alloys are widely used in aerospace, medical devices, automotive exhaust systems, chemical equipment and other fields due to their excellent strength-to-weight ratio, excellent corrosion resistance and good biocompatibility. Titanium welding, as the core technology in the titanium alloy manufacturing process, directly affects the structural integrity and performance of the product. Since titanium is extremely sensitive to oxygen and nitrogen, the welding process must be carried out under the protection of high-purity inert gas to ensure the quality of the weld and material properties.
Choosing the right welding method and equipment is the key to achieving efficient and precise titanium welding. Whether it is manual welding or automated production, titanium welding technology requires the operator to have professional knowledge and rich experience, and be equipped with advanced welding equipment and auxiliary tools.
Difficulties in welding titanium alloys
Titanium alloys are widely used in aerospace, chemical, medical and high-end manufacturing fields due to their excellent strength-to-weight ratio, corrosion resistance and high temperature performance. However, the welding process of titanium alloys faces many technical challenges, especially in controlling welding quality and structural performance. The following are the most common difficulties in titanium alloy welding:
High temperature oxidation and gas pollution
Titanium reacts easily with oxygen, nitrogen, hydrogen and other gases at high temperatures to form a brittle layer, which causes the weld to become brittle, discolored or even fail. If the shielding gas is impure or the weld area is exposed to the air during welding, blue, purple, gray or even white discoloration often occurs - this is a typical sign of weld oxidation. Therefore, controlling the purity and coverage of the shielding atmosphere is one of the key steps to ensure weld quality.
Thermal cracks and joint deformation
Titanium alloy has a small linear expansion coefficient and low thermal conductivity. During welding, heat is concentrated and the cooling speed is fast, which can easily cause thermal stress and cracks in the weld and heat-affected zone. Especially in the welding of plates and thin-walled pipes, welding deformation is very likely to occur due to local overheating or uneven cooling.
Changes in weld metallographic structure
Welding thermal cycles can easily lead to the coarsening of the titanium alloy weld zone, especially α+β titanium alloys (such as Ti-6Al-4V), which will produce hard and brittle phases due to the transformation of the post-weld structure, reducing the toughness and fatigue performance of the structure. For pressure vessels or aviation components that need to serve for a long time, weld metallographic control is particularly critical.
Dissimilar metal welding barriers
Direct welding between titanium and other metals such as steel, stainless steel, and aluminum is prone to generate a brittle intermetallic compound layer, which leads to deterioration of the mechanical properties of the joint. Such dissimilar metal connections usually require the introduction of intermediate transition materials or the use of special welding techniques such as explosive welding, laser welding, and diffusion welding to achieve reliable bonding.
Preparation and cleaning requirements before welding
In the titanium alloy welding process, the quality of the preliminary preparation directly determines the success or failure of welding. Even if advanced welding equipment and reasonable process parameters are used, if the pre-treatment is not in place, it will still cause defects such as weld contamination, pores and even slag inclusions, affecting the overall structural performance. The following is the preparation process that must be strictly followed before welding:
Welding area cleaning
Titanium alloys are extremely sensitive to pollution. Before welding, oil, moisture, oxide scale and other impurities in the welding area and at least 25mm around it must be removed:
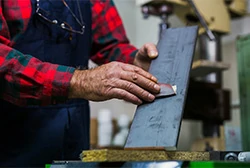
Mechanical cleaning
Stainless steel wire brush, emery cloth or oil-free lathe tool can be used for grinding to ensure that there is no visible oxide film on the surface.
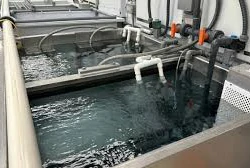
Chemical cleaning
Chlorine-free cleaning agent or anhydrous ethanol is often used to wipe the welding area and keep it dry.
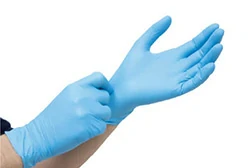
Glove and tool requirements
Operators must wear powder-free nitrile gloves, and all titanium-contact tools and fixtures should be clean and grease-free to prevent contamination.
Welding wire and filler material preparation
The welding wire or electrode used must match the base material and ensure that it is clean, dry and free of oil. It is usually recommended to use special titanium welding wire (such as ER Ti-2, ER Ti-5) and wipe it clean with anhydrous ethanol before use.
Gas protection system inspection
When using argon or helium as shielding gas, ensure that the gas purity is ≥99.99% and avoid using recycled gas or low-purity industrial gas. The shielding gas should be ventilated for 20-30 seconds before welding to exhaust the residual air in the system and check that there is no leakage in the gas supply pipeline.
Pre-installation and spot fixation process
For large titanium structures or thin-walled titanium parts, spot welding or fixture positioning should be used before welding to ensure the assembly accuracy of the joint and avoid fluctuations in weld quality due to assembly gaps or misalignment.
Common methods of titanium alloy welding
The choice of titanium alloy welding method depends on factors such as workpiece size, weld quality requirements, production efficiency and environment. The following are several welding technology solutions that are widely used and proven to be reliable in industry:
TIG welding (Tungsten Inert Gas Welding)
TIG welding is the most commonly used welding method for titanium alloys, especially for thin plates, pipes and places with high requirements for welds. This method is carried out under the protection of high-purity argon gas, with stable weld quality and small deformation, and is especially suitable for precision welding tasks such as titanium exhaust pipes, aerospace components, and medical implants.
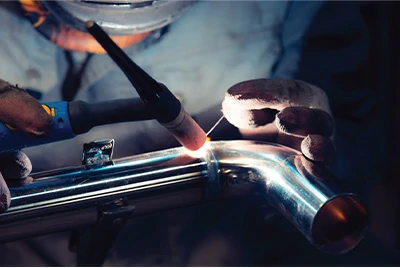
With the help of special equipment such as titanium TIG 200 and TIG foot pedal control system, the current intensity and molten pool shape can be accurately adjusted to improve controllability and forming consistency.
Laser welding
Laser welding is known for its high energy density and extremely small heat-affected zone, and is suitable for welding micro devices and structural parts with strict deformation requirements. Its non-contact, high-speed and precise characteristics make it suitable for automated production lines, such as microelectronics, medical equipment and other fields.
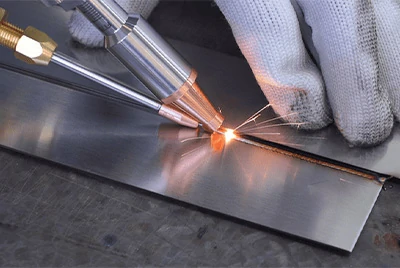
Laser technology can also be applied to dissimilar metal welding scenarios, such as the precision connection of titanium with stainless steel or aluminum. The growth of the interface reaction layer can be effectively controlled by optimizing parameters.
MIG welding (metal inert gas welding)
MIG welding is suitable for large-area connection of thick-walled titanium structural parts and has high deposition efficiency, but it has extremely high requirements for the shielding gas flow field and process control.
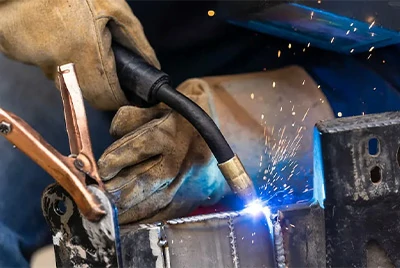
If the process is stable and the gas protection is good, MIG welding can also be used as one of the auxiliary means for mass production of titanium alloys.
Vacuum electron beam welding
It is suitable for connecting titanium alloy parts with high precision and high density requirements, such as aircraft engine components, aerospace equipment, etc.
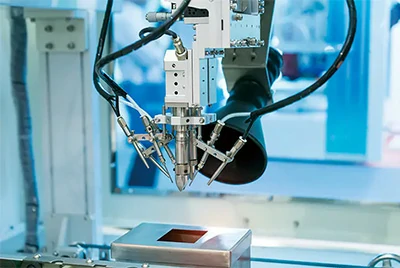
Vacuum electron beam welding is completed in a vacuum environment, avoiding interference from impurities in the air. The internal defects of the weld are extremely low, but the cost is high and the equipment requirements are high. It is often used in high-end manufacturing fields.
Dissimilar welding solutions for titanium alloys and common metals
Dissimilar welding of titanium alloys and other metals (such as stainless steel, aluminum, carbon steel, etc.) faces significant metallurgical challenges. Since titanium easily forms brittle intermetallic compounds with other metal elements (such as Fe and Al) at high temperatures, direct fusion welding usually results in low joint strength and high crack tendency. Solving this problem requires the combined use of multiple advanced welding processes and structural design methods.
Intermediate transition layer welding
By adding transition metals such as molybdenum, nickel, and copper as an intermediate layer, the direct reaction between titanium and other metals is effectively isolated to avoid the formation of brittle compounds. This technology is suitable for combinations such as titanium-steel and titanium-stainless steel, and is often used in the manufacture of pressure vessels and heat exchangers.
Explosive welding (explosive compounding)
The instantaneous high pressure generated by the explosion wave is used to promote the metal interface contact, forming a metallurgical bond in a non-melting state. It is widely used in the manufacture of composite structural materials such as titanium-steel composite plates.
Diffusion welding
Atomic diffusion bonding is achieved through long-term pressure in a high-temperature vacuum environment. It is suitable for occasions with extremely high requirements for structural integrity and weld density, such as space capsules, heat exchange components, etc.
Laser assisted welding
The high precision and low heat input characteristics of laser welding make it advantageous in welding dissimilar metals such as titanium and stainless steel, titanium and aluminum, etc. By controlling the laser focus and parameters, the thickness of the reaction layer can be precisely controlled.
Brazing and cold welding
Suitable for connecting small precision devices, such as electronic components, medical catheters, etc. Brazing usually combines thin metal foil or powder to achieve connection at medium temperature; cold welding is suitable for flexible contact interfaces.
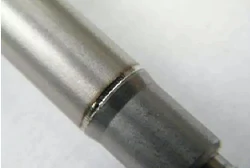
Titanium to stainless steel
Commonly used for chemical and medical equipment, suitable for intermediate layer, laser, or diffusion welding.
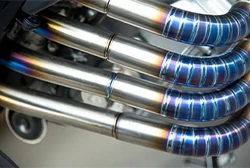
Titanium to aluminum
Ideal for lightweight structures and heat exchangers; explosion welding, brazing, or cold pressure welding recommended.
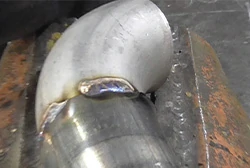
Titanium to steel
Commonly used in composite panels and supports, connected via explosive composite or intermediate layer technology.
Quality control and precautions in titanium alloy welding
Quality control is critical during titanium alloy welding. Since titanium is highly sensitive to gases such as oxygen and nitrogen, any slight operational error may cause weld embrittlement, discoloration or reduced strength. The following are key control points to ensure welding quality:
Cleaning and welding preparation
The titanium surface must be completely clean of oil, oxide layer and fingerprint residue. It is recommended to use chlorine-free cleaning agent and mechanical grinding and then wipe with a dust-free cloth. The welding wire and the workpiece surface should be kept clean to avoid the introduction of contaminants into the weld.
Tip: Pollution is the main factor causing welding defects. Before welding, the operation should be carried out in a clean and closed space as much as possible.
Protective gas cover
Use high-purity argon (purity ≥ 99.999%) as the shielding gas, and ensure that the welding area is always covered by argon before cooling, including the back of the weld (back protection). When TIG welding, a titanium-specific gas diffuser or a torch back-drag system should be used to avoid discoloration and oxidation of the weld.
Welding filler material selection
Titanium alloy welding should use filler metals that match or are compatible with the parent material. Common filler wires include ERTi-2, ERTi-5, ERTi-23, etc. When selecting, the parent material type, structural requirements and use environment should be considered comprehensively to avoid failure caused by strength mismatch or stress concentration.
Operational consistency and process stability
Ensuring the stability of welding current, voltage, and welding speed, and making fine adjustments through foot controls (such as TIG foot pedals) can effectively improve welding consistency. Automated or mechanized systems can also provide more stable welding quality in mass production.
Welding color and weld judgment
The color of the weld is an important appearance indicator for judging the quality of titanium alloy welding. Silvery white to golden yellow usually indicates sufficient shielding gas and good welding process control, while bluish purple, gray or dark colors may indicate excessive oxidation or protection failure. This color change reflects whether the welding process is contaminated by oxygen, nitrogen and other elements in the air.
Since titanium is extremely sensitive to atmosphere at high temperatures, the color of the weld becomes one of the primary criteria for quickly judging whether the welding is qualified on site. Although the color of the weld cannot fully reflect the welding strength or internal defects, in actual operation, it is the first checkpoint to ensure the effectiveness of welding protection.
Reference standards: AWS D17.1 and AMS 2801 have clear grades for titanium weld colors and can be used as a reference for production quality.
Titanium alloy welding equipment and process capabilities display
We are equipped with a complete titanium alloy welding process system and advanced equipment, covering a variety of common welding methods, including TIG welding, laser welding, diffusion welding, etc., which can meet various needs from single specimens to mass production.
TIG titanium welding equipment and configuration
We use TIG welding systems optimized for titanium materials. Representative equipment includes Titanium TIG 200 and other high-frequency pulse control models, with the following features:
- Stable low current arc starting performance, suitable for precision welding
- Dynamic current regulation with TIG foot pedal
- Equipped with efficient water cooling system and inert gas towing protection to avoid oxidation in the heat affected zone
Laser welding system
The laser welding station supports high energy density welding and is suitable for welding micro titanium components or dissimilar metal composite parts:
- Equipped with high-precision servo platform and beam focusing system
- Achieve low deformation and high consistency automated operation
- Especially suitable for laser welding of titanium and stainless steel interfaces
Special welding and auxiliary processes
We also have the following special welding and connection technology capabilities
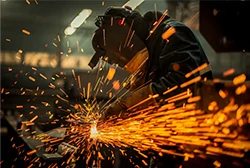
Diffusion welding and explosion welding
For composite panels or dissimilar metal structures
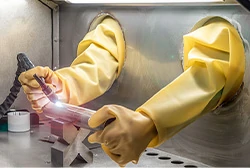
Vacuum environment protection welding
Suitable for welding quality control of key components
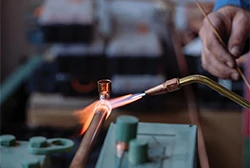
Small brazing and cold welding processes
Suitable for precision components and sample making
All equipment is equipped with a process monitoring system and can provide welding parameter recording, third-party certification and process traceability capabilities to ensure that the welding process is controllable and the results are reliable.
Chalcotitanium welding customization support and service advantages
As a professional titanium alloy material supplier, Chalcotitanium not only provides titanium products of various grades and specifications, but also has the supporting service capabilities to support customers in welding processing and finished product manufacturing. From material selection, welding suitability analysis, to cooperative processing resource matching, we are committed to helping customers achieve high-quality and efficient titanium alloy welding applications.
Titanium material selection and welding adaptation suggestions
- Provide titanium alloy raw materials suitable for different welding methods such as TIG, laser, diffusion welding, explosion welding, etc.
- Recommend suitable titanium material types, states and surface treatment methods according to customer product structure and welding process requirements
- We can provide titanium wire, titanium rod and other supporting materials for welding to ensure material consistency and weld compatibility
Finished product processing assistance and technical resource integration
- Support small batch sample proofing, customized welding parts development and other project cooperation models
- Provide welding process adaptation suggestions according to the application industry (such as chemical, medical, aviation)
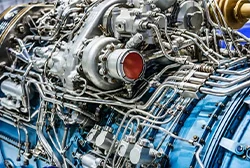
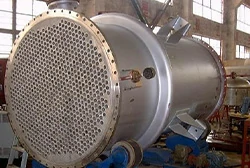
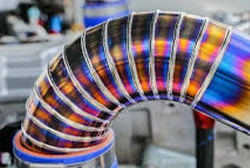
Technical consulting and long-term project support
We provide technical consulting services related to titanium alloy welding, covering common problems such as welding crack control, thermal deformation response, and weld quality improvement. At the same time, for large-volume or high-standard projects, we can cooperate with customers to carry out preliminary preparations such as material standard adaptation and welding performance verification, and support the customized development of special titanium material solutions for special processes (such as explosive welding, brazing, etc.). Please contact us for professional advice and material support to help you efficiently advance your titanium alloy welding project.