Platinized Titanium Anode
Updated : Jun. 24, 2025Platinum-coated titanium anode is an electrode material that uses titanium as the substrate and is coated on its surface with a layer of metallic platinum (Pt) through electroplating or pyrolysis methods.
It combines the strength and corrosion resistance of titanium with the high conductivity, catalytic activity, and corrosion resistance of platinum, and is widely used in various electrochemical and industrial electroplating environments.
Structure of Chalco titanium anode
Titanium substrate has high strength and good corrosion resistance, usually made of Grade 1 or Grade 2 titanium.
The platinum layer provides excellent electrical conductivity, catalytic activity, and outstanding chemical corrosion resistance.
The coating thickness generally ranges from 0.2 to 10 microns and can be customized according to specific usage environments.
Types of platinum-coated titanium anodes offered by Chalco
As a professional manufacturer of platinum-coated titanium anodes, Chalco is dedicated to providing high-performance, customized anode solutions for clients across various industries. We employ mature electroplating techniques and a strict quality control system to supply Pt/Ti anodes in various structural forms, including mesh, rod, plate, and tube types.
Below are the standard types of platinum-coated titanium anodes regularly offered by Chalco.
Platinum-coated titanium mesh anode
Made from industrial pure titanium perforated mesh or expanded mesh as the substrate, the surface is uniformly coated with a platinum layer. The porous structure facilitates electrolyte flow and gas release.
Contact us now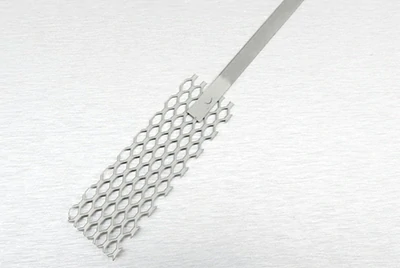
Common specifications include a coating thickness ranging from 0.1 to 20 microns, with an operating voltage not exceeding 24 volts and a maximum current density of up to 7500 amperes per square meter. The applicable pH range is from 1 to 12, and the working temperature is below 60°C. The titanium substrate thickness typically ranges from 0.5 mm to 2.0 mm, with customizable dimensions such as 50×100 mm, 100×200 mm, and other specifications.
The product uses perforated or expanded titanium mesh, optimized for aperture size and open area ratio, which increases the contact area between the electrolyte and the anode by more than 50%, thereby improving the uniformity of current distribution. After high-temperature electroplating of the platinum layer, the entire anode is processed in a vacuum sintering furnace at temperatures exceeding 1200°C, ensuring a stronger bond between the platinum atoms and the titanium surface. As a result, the coating’s detachment rate is extremely low—less than 0.01% per year.
In addition, the mesh structure design facilitates the rapid release of chlorine and oxygen gases, reducing bubble coverage on the electrode surface by approximately 30%, which significantly enhances electrolysis efficiency.
These electrodes are typically used in electroplating industries such as chrome, gold, and rhodium plating. They are also widely applied in chlor-alkali electrolysis, electrolytic water treatment, and sodium hypochlorite generators, and are suitable for use in laboratory electrolytic cells as well.
Platinum-coated titanium rod anode
Using solid titanium rods as the substrate, the entire surface is coated with a platinum layer. It is suitable for deep holes, cylindrical equipment, or confined spaces.
Contact us now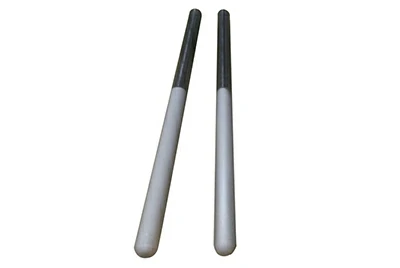
In terms of specifications, the diameter typically ranges from Φ10 mm to Φ50 mm, with lengths available in 100 mm, 200 mm, 500 mm, and other sizes, and can also be customized as needed. The platinum coating thickness generally ranges from 0.1 microns to 20 microns.
The product is made from industrial pure titanium rods with diameters from Φ3 to Φ10 mm, offering a flexural strength of 275 MPa or higher, making it particularly suitable for high-pressure or buried environments. The structure is robust and capable of supporting long-term continuous operation.
To reduce costs and improve electrical efficiency, the platinum layer is usually applied only to the portion inserted into the liquid. Precision spraying and segmented electroplating techniques are used to ensure uniform coating thickness and clear boundaries.
In addition, the product supports customized multi-point array insertion anode designs, effectively increasing coverage efficiency for buried or pipeline protection. The anodes are evenly distributed, resulting in more stable protective current density.
Typical applications include cathodic protection systems such as offshore platforms and storage tanks, precision electroplating fixtures, and gas diffusion anode structures..
Platinum-coated titanium plate anode
Using flat titanium plates as the anode substrate, suitable for large-area, high current density electrolysis conditions.
Contact us now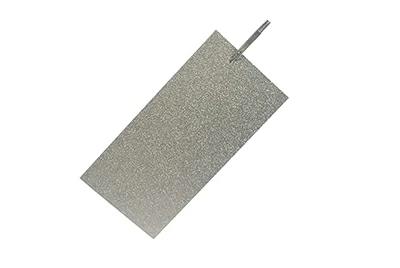
Using flat titanium plates as the anode substrate, suitable for large-area, high current density electrolysis conditions.
In terms of specifications, the thickness options typically include 1.0 mm, 1.5 mm, 2.0 mm, and 3.0 mm, with customizable sizes such as 100×200 mm and 300×500 mm. The platinum coating thickness generally ranges from 2.5 microns to 10 microns.
The product undergoes rolling and straightening processes to ensure a smooth titanium plate surface, with surface flatness controlled within 0.1 mm. This helps achieve uniform current distribution and prevents local overcurrent-induced erosion.
Using multiple pulse electroplating technology, the platinum layer can be plated within the 2.5 to 10 micron thickness range, increasing coating density by over 40% and significantly extending corrosion resistance life.
The edges are treated with localized edge-wrapping sintering processes to effectively prevent coating edge peeling and improve product durability.
Typical applications include hard chrome plating, printed circuit board electrolytic etching, and anode plates for chemical reaction tanks..
Platinum-coated titanium wire anode
Titanium wire anode uses high-purity titanium fine wire as the substrate, with a platinum coating thickness of 0.1–20 μm. It offers good flexibility and stable conductivity, suitable for small electrolysis equipment, precision electroplating, laboratory electrochemistry, and similar applications.
Contact us now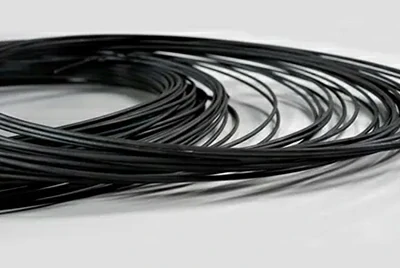
Titanium wire anode uses high-purity titanium fine wire as the substrate, with a platinum coating thickness of 0.1–20 μm. It offers good flexibility and stable conductivity, suitable for small electrolysis equipment, precision electroplating, laboratory electrochemistry, and similar applications.
In terms of specifications, common titanium wire diameters are Φ0.5 mm, Φ1.0 mm, and Φ2.0 mm, with customization available upon request. The titanium wire can be supplied in coil form or as straight-cut lengths, with a platinum coating thickness ranging from 0.1 to 20 microns.
The product features strict control of the titanium wire outer diameter between 0.5 and 2.0 mm and a high platinum coverage rate. It is processed using a micro-current electroplating technique, suitable for precise control of the electric field. The platinum coating is applied evenly 360 degrees on a continuous plating line, combined with a tension control system to ensure uniform coating thickness and strong adhesion, resistant to peeling or cracking.
This product can achieve current response accuracy within ±1% in applications such as microchannel reactors and electrolytic microelectrodes, meeting high-precision requirements.
Typical applications include small electrolytic devices, conductive coils for electroplating, and consumable anodes for scientific research experiments.
Platinum-coated titanium tube anode
Hollow titanium tube structure, capable of housing a cooling system or directing fluid flow, suitable for complex reaction environments with high temperature and high flow rates.
Contact us now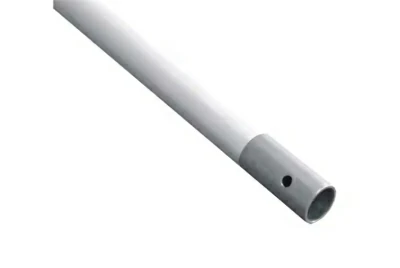
Hollow titanium tube structure, capable of housing a cooling system or directing fluid flow, suitable for complex reaction environments with high temperature and high flow rates.
In terms of specifications, the outer diameter ranges from Φ10 mm to Φ200 mm, with a wall thickness between 1.0 and 2.5 mm. The platinum coating thickness is typically 1 to 5 microns. The applicable pH range is from 1 to 12, and the current density does not exceed 7500 amperes per square meter.
The hollow titanium tube structure features internal cooling fluid channels, which can control the anode temperature below 60°C during high-temperature electrolysis reactions, extending the coating lifespan by 1.5 to 2 times. The end seals of the anode tube use titanium/platinum composite powder pre-sintered caps, effectively preventing edge pitting or cold soldering issues and avoiding coating peeling.
This structure has a pressure resistance strength of up to 1.5 MPa, making it suitable for high-pressure PEM electrolyzers and specialized chemical reaction equipment.
Typical applications include PEM electrolyzers, industrial-scale large electrolyzer anode assemblies, as well as hydrogen production and precious metal recovery systems.
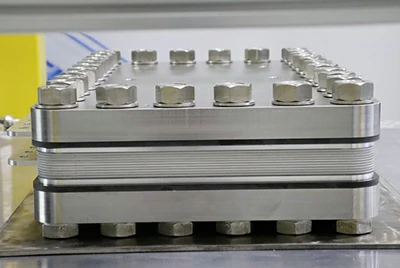
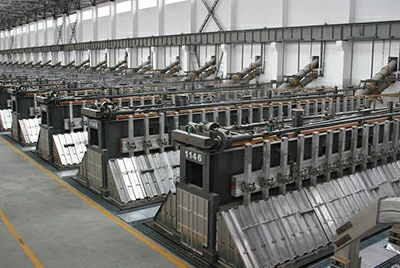
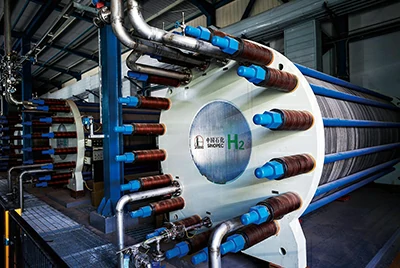
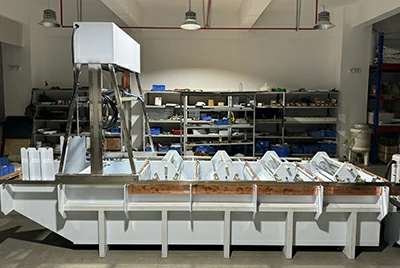
Why are platinum-coated titanium anodes superior to traditional lead anodes?
Platinum-coated titanium anodes are widely used in various electrochemical environments due to their outstanding corrosion resistance, high-temperature tolerance, and stable electrical conductivity. Compared to traditional lead anodes, they offer more stable performance, longer service life, and structural advantages that allow sustainable use, providing users with more efficient, environmentally friendly, and cost-effective solutions.
More cost-effective
Platinum-coated titanium anodes deliver electrochemical performance comparable to pure platinum or gold anodes but at significantly lower material costs, greatly reducing equipment investment and operating expenses.
Excellent overpotential characteristics
They exhibit high overpotential for oxygen evolution reactions, effectively preventing side reactions, and low overpotential for hydrogen evolution reactions, thereby improving overall electrolysis efficiency and reaction selectivity.
Reusable titanium substrate
When the surface platinum layer is consumed, the titanium substrate can still be reused. By re-electroplating, the anode performance can be restored, extending the service life and reducing long-term procurement costs, aligning with green manufacturing principles.
High current density bearing capacity
With a sturdy structure, these anodes can stably withstand high current density operation, suitable for heavy-duty or continuous industrial electrolysis environments, ensuring consistent production output.
Uniform conductivity and dimensional stability
The entire anode maintains consistent conductivity without surface unevenness or localized failure over time, making it especially suitable for applications requiring high dimensional stability, such as electrochlorination and electrolytic water treatment.
How does Chalco ensure the high quality of platinum-coated titanium anodes?
At Chalco, we consistently adhere to the highest quality standards in manufacturing every platinum-coated titanium anode, ensuring outstanding performance and long-term stable operation in various industrial electrolysis environments.
To fulfill this commitment, we have established a rigorous and quantifiable quality control system covering the entire process, including materials, manufacturing, performance, and lifespan testing.
Before shipment, each batch of products undergoes comprehensive testing on the following key aspects. Only when all indicators meet the standards will the products be approved for delivery, truly achieving "quality verified by testing, and customers protected by standards.”
Test item | Test conditions | Acceptance criteria |
Coating adhesion test | Repeated peeling with 3M tape | No black marks on tape; no coating peeling |
Bend integrity test | Bending 180° around a Φ12 mm mandrel | No cracks or peeling at the bend |
Coating uniformity evaluation | X-ray fluorescence spectrometer (XRF) | Thickness deviation ≤15% |
Coating thickness measurement | XRF detection | 0.1–15 μm, customized per customer requirements |
Chlorine evolution potential test | 2000 A/m², 25°C, saturated NaCl solution | Potential ≤1.15 V |
Polarization rate test | Voltage change tested at 200~2000 A/m² | Potential fluctuation ≤40 mV |
Lifespan test | 40,000 A/m², 1 mol/L H₂SO₄, 40°C, continuous electrolysis | Service life ≥150 hours (1 μm Pt coating) |
Corrosion weight loss test | 20,000 A/m², 8 mol/L NaOH, 95°C, 4 hours electrolysis | Mass loss ≤10 mg |
Through this systematic testing process covering structure, performance, and lifespan, Chalco not only ensures that every anode possesses key qualities such as high adhesion, stable potential, corrosion resistance, and long service life, but also truly fulfills its brand promise of "ready to use upon delivery, quality you can trust.”
We believe testing is not just about passing standards, but about leading the industry. It is this commitment to high standards that has earned Chalco’s platinum-coated titanium anodes the long-term trust of customers across industries including electroplating, chlor-alkali, chemical, and energy sectors.
How to choose the right platinum-coated titanium anode?
Understand electrolyte composition
The chemical nature of the electrolyte determines the corrosion resistance required for the anode.
In chlorine-containing environments (such as NaCl or HCl systems), choose anodes with thick platinum coatings (5 μm) to resist severe corrosion.
Avoid using unprotected Pt/Ti anodes in fluoride-containing or strong oxidizing environments to prevent substrate damage.
Optimize current density
Excessive current density can cause local overheating of the anode, uneven coating, or peeling.
It is generally recommended to keep the operating current density ≤ 75 A/dm².
For higher currents, select thicker platinum coatings or use multiple parallel anodes for uniform current distribution.
Control operating temperature
Anode stability is closely related to solution temperature.
Keep operating temperature ≤ 60°C to prevent platinum layer detachment or titanium substrate corrosion.
For high-temperature electrolysis (>80°C), use internally cooled titanium tube anodes or design system cooling measures.
Assess impurities in the working environment
Contaminants like sulfur, fluorine, and heavy metal ions accelerate anode aging.
Conduct a thorough evaluation of electrolyte impurity sources before selection.
If necessary, opt for protective layer designs or partial platinum plating to reduce corrosion risk in sensitive areas.
Customize structure type according to application
Different anode structures fit different scenarios:
Titanium mesh anodes are suitable for large-area uniform plating with fast gas release.
Titanium rod anodes are ideal for insertion use in confined spaces requiring point-to-point electrolysis.
Titanium plate and screen anodes handle high currents well, commonly used in fixed tank setups.
Titanium wire anodes suit precision plating and small equipment, offering good flexibility for complex environments.
Match the suitable pH range
Platinum-coated titanium anodes typically work in pH 0–11 environments.
For processes with stricter pH requirements, verify material compatibility.
Consider anode lifespan and replacement cycle
A 2.5 μm platinum layer generally meets the needs of neutral or mildly acidic environments, with a lifespan of 1 to 3 years.
At 5 μm thickness, anodes are better suited for highly corrosive environments, lasting 5 to 7 years or more.
For long project cycles, choose re-platable designs to reduce maintenance costs.
Evaluate budget and long-term return
Although high-quality platinum-coated titanium anodes have higher initial costs, their longer service life, lower replacement frequency, and higher electrolysis efficiency significantly reduce overall operating costs in the medium to long term.
Chalco platinum-coated titanium anode safe use guide
To ensure the efficient and stable operation of Chalco platinum-coated titanium anodes in various industrial electrolysis applications and to extend their service life, users should follow the key safety and usage guidelines during operation and maintenance. As precision electrode devices, the anodes are composed of a high-purity titanium substrate with a uniform and dense platinum coating. Physical damage and chemical corrosion must be avoided to guarantee their performance and safety.
Before use
Before use, please inspect the anode surface to ensure there are no obvious scratches, cracks, or peeling, maintaining surface integrity. Confirm the compatibility of the electrolyte; it is strictly prohibited to use the anode in electrolytes containing fluoride ions (F⁻), bromide ions (Br⁻), cyanide (CN⁻), or other highly corrosive or toxic substances, as these ions can damage the platinum coating and pose safety risks. When starting the electrolysis system, the current should be gradually increased step by step to avoid sudden high voltage on the electrode, which may cause stress damage to the coating.
Operation guidelines during use
It is recommended to keep the anode’s working current density within the design range, usually not exceeding 75 amperes per square decimeter, to avoid local overheating and accelerated platinum layer consumption caused by excessive current. The power supply should have stable voltage and current regulation to ensure the current and voltage remain steady, preventing fluctuations that could adversely affect the electrode’s performance and lifespan. Inside the electrolytic cell, avoid direct contact between the anode and hard objects such as metal hooks or clamps, to prevent scratching or cracking of the platinum coating and protect the anode’s surface integrity.
Maintenance and storage after use
After each use, clean the anode surface with pure water or a neutral cleaning solution to remove attached impurities, deposits, or crystals. After cleaning, place the anode in a cool, ventilated area to air dry naturally, or gently wipe it dry with a clean, lint-free cloth. Avoid prolonged soaking or storage in humid conditions. When not in use, keep the anode away from high-temperature heat sources and high-voltage equipment to prevent accidental short circuits or thermal damage to the material.
Chalco always places customer safety as the top priority and strictly adheres to the highest quality and durability standards for platinum anodes. If you have any questions or concerns about the safe use of platinum anodes, our expert team is always available to assist you.
For more information about our products and how we meet your electrochemical needs, please feel free to contact us.