Titanium Tube Sheet
Updated : Jun. 27, 2025Is your heat exchange equipment suffering from corrosion, premature failure, and high maintenance costs? In demanding environments like chemical processing, desalination, and power generation, traditional materials often fall short of your safety and longevity requirements.
Chalco Titanium offers high-performance Titanium Tube Sheets and explosion-welded Titanium Clad Tube Sheets compliant with ASTM B265/B898 standards. Leveraging titanium's exceptional corrosion resistance, high strength, and temperature adaptability, we fundamentally solve traditional material pain points, ensuring your equipment operates stably, efficiently, and durably, significantly cutting maintenance and downtime expenses. Choose Chalco Titanium for unparalleled reliability and an ultra-long service life for your heat exchange equipment.
What is a Titanium Tube Sheet?
A titanium tube sheet is a core component in heat exchangers, condensers, and other pressure vessels. It's a precisely machined flat plate featuring accurately drilled holes arranged in a specific pattern, designed to fix and support the ends of heat exchange tubes. Tubes are securely connected to the tube sheet via expansion or welding, effectively isolating different fluid media and maintaining the equipment's internal design pressure.
Its key functions include:
- Structural Support: Acting as a crucial support for the heat exchanger tube bundle, ensuring precise tube positioning and alignment.
- Sealing and Isolation: Providing a vital sealing barrier that effectively prevents mixing between tube-side and shell-side fluids, guaranteeing safe and efficient heat exchange.
The machining precision of the tube sheet (hole position, diameter) directly impacts the reliability and sealing of the tube-to-tube sheet connection, which is critical for the equipment's assembly quality, long-term operational reliability, and even heat transfer efficiency.
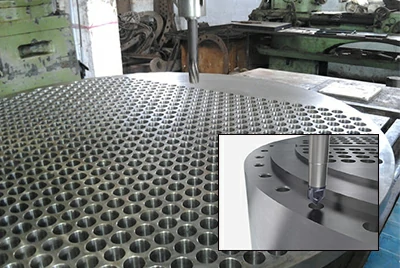
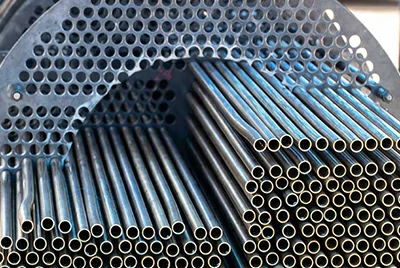
Titanium Tube Sheet
Titanium tube sheets are integrally formed from a single material—either commercially pure titanium or titanium alloys—via casting, forging, and precision machining. They contain no dissimilar metal layers and are composed entirely of titanium metal.
Contact us now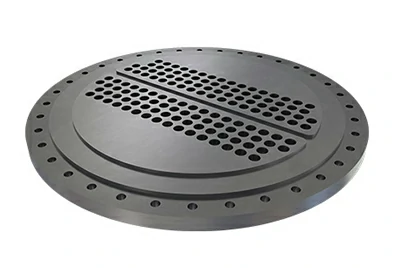
Specifications
Alloy: Gr.1, Gr.2, Gr.3, Gr.5, Gr.7, Gr.12
Thickness: 20-100 mm
Diameter: Φ400-Φ3000 mm, customizable
Hole Diameter: Φ16, Φ19, Φ22, Φ25, Φ32 (Tolerance: ±0.15 mm)
Hole Verticality: ≤0.25 mm
Flatness: ≤0.2 mm/m
Surface Roughness: Ra≤6.3μm / Ra≤3.2μm
Standards: ASTM B265, ASTM B381
Product Types
-
Pure Titanium Tube Sheet Gr.1, Gr.2, Gr.3
Forged or rolled from pure titanium without dissimilar metal layers, these sheets resist seawater and acid-alkali corrosion, lasting over 20 years—ideal for titanium tube sheets.
-
Titanium Alloy Tube Sheet Gr.5, Gr.7, Gr.12
Forged at high temperatures and heat-treated, these alloys reach ~1000 MPa tensile strength with excellent resistance to heat, pitting, and stress corrosion—ideal for reducing acids and high-pressure, high-temp use.
Key Features
1. Outstanding corrosion resistance in acidic, alkaline, saline, and chloride-rich environments.
2. Homogeneous structure and performance, eliminating the risk of interface delamination.
3. Excellent plasticity and weldability in commercially pure grades, facilitating tube expansion and welding processes.
Typical Applications
Widely used in highly corrosive environments where material purity and corrosion resistance are critical, and cost constraints are secondary. Typical fields include chlor-alkali industry, pharmaceutical-grade pure water systems, and high-end petrochemical equipment.
Titanium Clad Tube Sheet
Titanium clad tube sheets are bimetallic composites combining a titanium surface with a carbon or stainless steel base via explosive welding or hot rolling, offering titanium’s corrosion resistance with the strength and cost benefits of the substrate.
Contact us now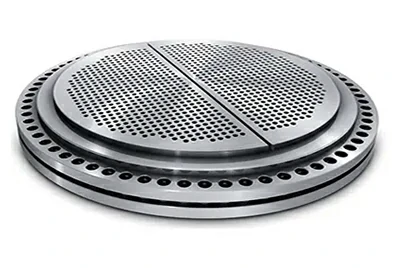
Specifications
Titanium Cladding Thickness:1.5 - 16 mm
Base Material Thickness:3 - 200 mm
Max Dimensions:2 m × 6 m
Cladding Methods:Explosive Bonding, Hot Rolling
Hole Diameter:Φ16, Φ19, Φ22, Φ25, Φ32 (Tolerance: ±0.15 mm)
Hole Pitch:1.5 - 2× hole diameter
Array Patterns:Triangular, Rotated Triangular, Square, Rotated Square
Hole Verticality:≤0.25 mm
Flatness:≤ 0.2 mm/m
Surface Roughness:Ra≤6.3μm / Ra≤3.2μm
Standards:ASTM B898, ASTM A264, JIS G3603, GB/T 8547-2019, ISO 18273
Product Types
-
Titanium–Carbon Steel Clad Tube SheetCladding Alloys: Gr.1, Gr.2, Gr.7, Gr.12
Base Materials: Q235B, Q345R, Gr.60, Gr.70
Combines the excellent corrosion resistance of titanium with the high strength and cost-efficiency of carbon steel, ideal for petrochemical, power generation, and seawater desalination systems where corrosion resistance and pressure-bearing capacity are both critical.
-
Titanium–Stainless Steel Clad Tube SheetCladding Alloys: Gr.1, Gr.2, Gr.7, Gr.12
Base Materials: SUS3304, 316L, 317L, Duplex Stainless Steels 2205 / 2507
Enhances pitting and crevice corrosion resistance, while maintaining structural strength of stainless steel. Suitable for pharmaceutical, food processing, and fine chemical industries requiring high cleanliness and corrosion-resistant heat exchanger or pressure vessel components.
Key Features
- The titanium surface layer delivers corrosion resistance on par with solid titanium, effectively withstanding seawater, acidic, alkaline, and crevice corrosion.
- The carbon steel or stainless steel substrate provides mechanical strength for large-diameter and high-pressure tube sheet applications.
- Hot rolling or explosive welding forms a dense metallurgical bond at the interface with no pores or impurities; tensile shear strength reaches 250–350 MPa.
- The titanium layer requires only a few millimeters to deliver full corrosion protection, significantly reducing material and processing costs compared to solid titanium sheets.
- The wavy bonding interface enhances fatigue strength and impact resistance, ensuring long-term structural integrity in demanding environments.
Typical Applications
Titanium clad tube sheets are widely used in chemical and petrochemical systems (e.g., sulfuric acid, chlor-alkali, evaporators), seawater desalination, offshore platforms, power plant condensers, and food-grade heat exchangers. They also perform well in marine cooling, flue gas desulfurization, pulp processing, and large HVAC systems—offering an ideal mix of corrosion resistance, strength, and large-format fabrication for heat exchangers and pressure vessels.
Cladding Methods
-
Hot-Roll CladdingTitanium Cladding Thickness: 1 - 8 mm
Base Material Thickness: 3 - 200 mm
In hot-roll cladding, titanium and steel substrates are heated and rolled under high pressure, removing oxides and forming a strong metallurgical bond. The flat, dense, porosity-free interface offers high tensile and shear strength, ideal for large-scale production of titanium clad plates up to 6 m × 15 m.
-
Explosive Welding CladdingTitanium Cladding Thickness: 1.5 - 12 mm
Base Material Thickness: 3 - 150 mm
Explosive welding uses controlled detonation to propel titanium onto a steel base at supersonic speed, forming a wavy metallurgical bond with shear strength up to 350 MPa. It’s ideal for tube sheets in chemical processing, desalination, and high-pressure equipment requiring fatigue and impact resistance.
Why Choose Titanium Tube Sheets Over Other Metals?
1. Titanium forms a dense, self-healing TiO₂ film, resisting chloride, pitting, crevice, and stress corrosion far better than stainless steel or copper alloys.
2. With a density of 4.5 g/cm³ and tensile strength from 345 to 950 MPa, titanium offers a superior strength-to-weight ratio, ideal for lightweight, pressure-resistant tube sheets.
3. Pure titanium performs well from -250 °C to 250 °C, while high-strength alloys (e.g., Gr.5) handle 350–400 °C short-term, suiting most heat exchangers.
4. Though thermal conductivity is lower than copper or steel, thin walls and large transfer areas ensure high efficiency. With over 20 years’ service life and low maintenance, titanium cuts lifecycle costs.
5. Non-magnetic, non-toxic, and releasing almost no metal ions, titanium is ideal for ultra-clean heat exchangers in pharma, food, and semiconductors.
6. In nuclear power, desalination, desulfurization, pulp processing, and offshore use, titanium’s low activation, radiation, and fiber corrosion resistance ensure stable long-term performance.
Chalco Titanium Tube Sheet Gallery


Typical Applications of Titanium Tube Sheets
Heat Exchanger Equipment
In seawater desalination, titanium tube sheets in multi-stage flash evaporators and heat exchangers resist corrosion in high-salinity and chloride-rich environments for years, significantly reducing maintenance costs.
In power generation, titanium tube sheets are used in thermal power plant condensers, boiler cooling water systems, and flue gas desulfurization units. Their low activation and radiation resistance make them highly favored in nuclear power plant condensers.
In the chemical industry, titanium tube sheets ensure long-term stable operation in chlor-alkali, electroplating, sulfuric acid, nitric acid, PTA, and petrochemical reactors, evaporators, and condensers exposed to highly corrosive media.
In marine engineering and shipping, titanium tube sheets are used in ship seawater cooling systems, ballast water treatment, and offshore platform heat exchangers, offering excellent corrosion resistance against harsh marine environments.
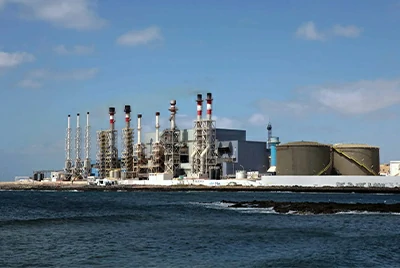
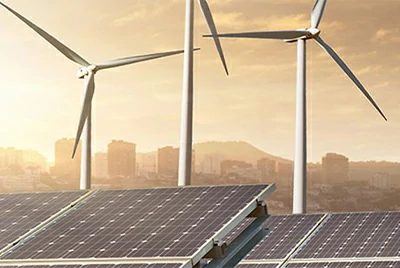
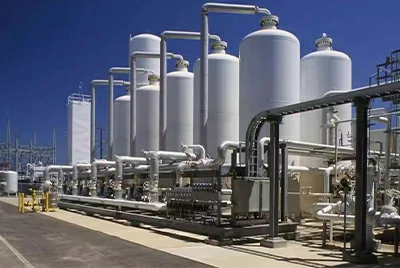
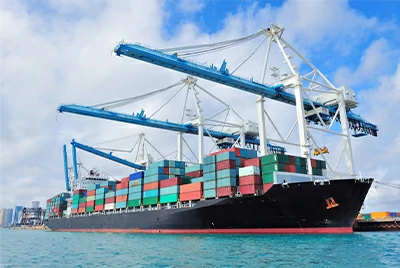
Pressure Vessels and Pipeline Systems
Serving as support components and sealing interfaces, titanium tube sheets provide outstanding structural strength and corrosion protection in high-pressure tanks, reactors, and corrosive pipelines across chemical, petroleum, and pharmaceutical industries.
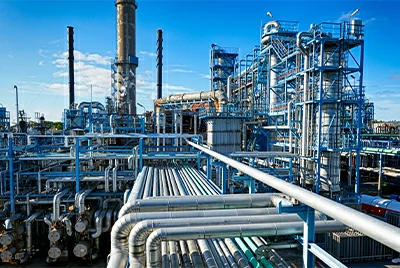
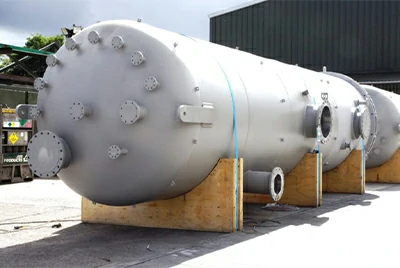
Pharmaceutical, Food, and Electronics Industries
In applications demanding ultra-high cleanliness and non-toxicity, such as pure water production, food and beverage processing, and electronic chip manufacturing heat exchange systems, titanium tube sheets ensure zero metal ion release, safeguarding product quality and process safety.
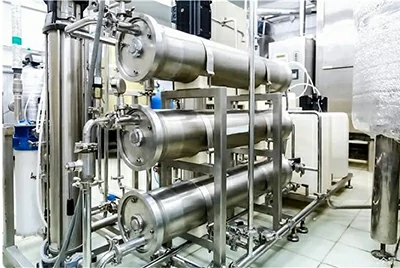

Precision Manufacturing of Titanium Tube Sheets
Raw Material Preparation and Initial Processing
Chalco Titanium sources premium titanium ingots and plates from top suppliers like Baoti Group, Western Superconducting, and TIMET. They conduct thorough chemical and mechanical testing, then perform forging or rolling followed by solution annealing to relieve stresses and optimize grain structure.
Core Processing: Precision Drilling Technology
- Utilizes high-precision CNC deep hole drilling machines and gantry drilling centers to ensure one-pass formation of tube holes.
- Supports hole patterns including triangular, rotated triangular, square, and rotated square arrays.
- Strict control of hole diameter tolerance at ±0.15 mm, hole wall roughness Ra ≤6.3 μm, with precise control over hole pitch and perpendicularity for tight assembly.
- To address titanium's hardness and low thermal conductivity, sharp carbide tools, low speed with high feed rates, and high-pressure cooling chip removal techniques are applied.
Joining and Surface Treatment Processes
Tube expansion is performed using mechanical or hydraulic methods with precise control of expansion amount (4–5% of tube wall thickness) to ensure a tight seal.
Preferred welding methods include tungsten inert gas (TIG) welding and laser welding, following a "expand then weld” procedure. Copper blocks are inserted inside tubes during welding to reduce deformation.
Pre-weld surface preparation involves removing oxide scale with stainless steel wire brushes, degreasing with acetone, and acid pickling with HF–HNO₃ mixture; post-weld treatment includes solution annealing and nitric acid passivation.
Comprehensive Non-Destructive Testing (NDT)
Ultrasonic testing (UT), radiographic testing (RT), eddy current testing (ET), penetrant testing (PT), and visual inspection are performed on tube sheets and welds to ensure absence of delamination, porosity, cracks, and other defects, confirming strong metallurgical bonding at the composite interface.
Why Choose Chalco Titanium's Titanium Tube Sheets?
Industry-Leading Experience and Expertise
Chalco Titanium specializes in titanium materials and products, especially titanium tube sheets and titanium-steel/stainless steel composites. With mature processes and project experience, we handle diverse, complex conditions.
Advanced Production Facilities and Processing Capabilities
Equipped with CNC deep hole drilling, gantry machining, explosive welding, laser welding, and non-destructive testing, Chalco Titanium covers all steps from raw material to finished product, meeting customization needs for titanium tube sheets.
Standardized Quality Control System
Certified ISO 9001:2015, production follows ASTM B265, B381, B898 standards. Each product undergoes detailed dimensional checks and non-destructive testing to ensure specs and reliability.
Comprehensive Customized Solutions
From pure titanium grades like Gr.2, Gr.7 to titanium-steel composites, we tailor materials and designs based on media, temperature, pressure, and service life, supporting detailed drawings and technical communication.
Outstanding After-Sales Service and Technical Support
We provide one-stop services including material advice, structural optimization, processing coordination, and logistics, with long-term technical support to ensure reliable, efficient heat exchange operation.
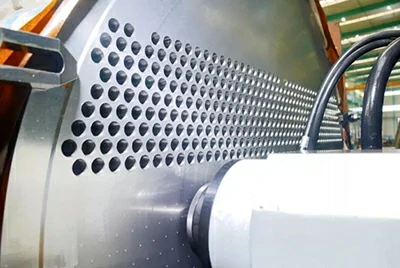
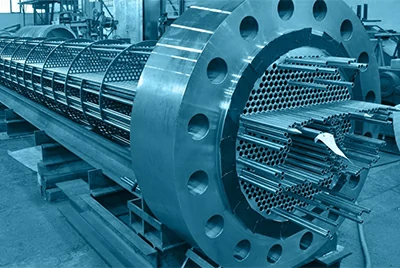

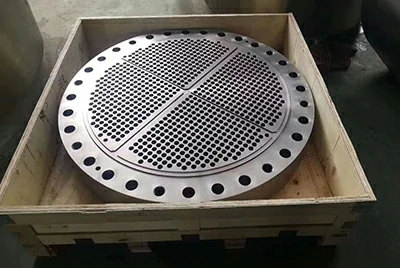
How To Choose Titanium Tube Sheets?
When selecting titanium tube sheets, assess the medium's corrosiveness, system pressure, temperature, and budget. Choose the titanium grade or composite that best balances corrosion resistance, strength, and cost-effectiveness.
Common Titanium Grades and Their Characteristics
- Gr.1 (TA1 Pure Titanium): Best ductility and corrosion resistance, ideal for highly corrosive environments like wet chlorine and chlor-alkali.
- Gr.2 (TA2 Pure Titanium): Balanced strength and corrosion resistance, preferred for seawater and general chemical media heat exchangers.
- Gr.5 (Ti-6Al-4V): Tensile strength near 950 MPa, suitable for high-pressure or heavy load structural applications.
- Gr.7 (Ti-0.2Pd Titanium Alloy): Best protection against reducing acids (sulfuric acid, hydrochloric acid), pitting, and crevice corrosion.
- Gr.12 (Ti-0.3Mo-0.8Ni Titanium Alloy): Maintains excellent strength and corrosion resistance in high-temperature chloride environments.
Titanium Composite Tube Sheet Material Combinations
- Cladding materials typically use grades Gr.1, Gr.2, Gr.7, Gr.12.
- Base materials include carbon steel (Q235, A516 Gr.70) or stainless steel (304, 316L, 2205, 2507, etc.).
- Example: Carbon steel base 34 mm + pure titanium cladding 5 mm.
How To Choose The Right Grade?
1. For seawater or mildly corrosive media, prioritize Gr.2 pure titanium tube sheets.
2. For high load or structural strength requirements, select Gr.5 titanium alloy tube sheets or increase the titanium cladding thickness in pure titanium composite sheets.
3. For strong acid or high-temperature corrosive environments, choose Gr.7/Gr.12 titanium tube sheets or composite structures with thicker titanium layers.
4. For cost-sensitive projects needing corrosion resistance, opt for titanium-carbon steel composite tube sheets to balance strength and economy.
5. For additional cleanliness or base material corrosion resistance, recommend titanium-stainless steel composite tube sheets for dual protection.
6. For professional material selection advice, contact our engineers anytime for personalized support.
Frequently Asked Questions (FAQ)
What Is The Typical Delivery Time For Titanium Tube Sheets?
The standard delivery time for pure titanium tube sheets is typically 4–6 weeks. For composite tube sheets (titanium-steel/titanium-stainless steel), delivery usually takes 6–8 weeks, depending on thickness and size. Expedited production services are available based on project deadlines and production capacity.
Do You Offer Small Batch Customization Services?
We support small batch and sample customization, accepting orders from single prototypes to mass production, maintaining consistent professionalism and cost-effectiveness in technical solutions and pricing regardless of order volume.
How Do You Assess The Interlayer Bond Strength And Verify Reliability?
In addition to standard tensile and shear tests, we perform in-plane peel tests on composite tube sheet samples and use metallographic microscopy to inspect the bonding interface. Bond strength must meet or exceed ≥250 MPa for rolling and ≥350 MPa for explosion welding before shipment.
How Is The Welding Quality Of Titanium Tube Sheets Ensured?
Using a "roll-expand then weld” process, we perform surface pretreatment before welding (brushing, degreasing, acid pickling). During welding, strict control of argon shielding and heat input is maintained. Post-weld, solution annealing and comprehensive nondestructive testing (UT/RT/PT) ensure welds are strong and crack-free.
Do You Provide Post-Weld Heat Treatment And Stress Relief Services?
For large tube sheets or titanium alloy tube sheets, we offer solution annealing after welding (600–800℃, holding for 1–2 hours) to relieve welding stresses. When necessary, aging treatments are also applied to optimize the microstructure.
How Is Galvanic Corrosion Prevented In Multi-Metal Systems With Titanium Tube Sheets?
When titanium contacts carbon steel or stainless steel, we recommend using insulating gaskets, electrophoretic coatings, or PTFE (polytetrafluoroethylene) washers as isolation measures. Additionally, construction processes are adjusted based on the medium’s pH and conductivity to prevent localized electrochemical corrosion.