Titan-3D-Druck: Vorteile, Technologien und Anwendungen
Aktualisierte : Jul. 2, 2025Wenn Titan auf 3D-Druck trifft, kommen Festigkeit, Korrosionsbeständigkeit und Designfreiheit zusammen – und machen Raketen, Implantate, Rennteile und Elektronik leichter, stabiler und individueller.
Dieser Leitfaden erklärt, warum Titan für den 3D-Druck geeignet ist, hebt Schlüsseltechnologien hervor und zeigt, wo es eingesetzt wird – und hilft Ihnen zu sehen, ob es für Ihr nächstes Hochleistungsprojekt geeignet ist.
Warum Titan für den 3D-Druck geeignet ist
Die traditionelle Bearbeitung ist eine Herausforderung
- Die geringe Wärmeleitfähigkeit von Titan führt zu schnellem Werkzeugverschleiß und geringer Effizienz in der CNC-Bearbeitung.
- Herkömmliche Methoden verschwenden viel Material, und Titan ist teuer – was die Produktionskosten in die Höhe treibt.
Der 3D-Druck reduziert Materialverschwendung und steigert die Effizienz, was ihn zu einer intelligenteren Art der Herstellung von Titanteilen macht.
Hervorragende Materialeigenschaften
- Sein hohes Verhältnis von Festigkeit zu Gewicht macht es ideal für leichte, hochfeste Bauteile.
- Eine hervorragende Biokompatibilität unterstützt den Einsatz in Implantaten und Medizinprodukten.
- Die überlegene Korrosionsbeständigkeit gewährleistet eine langfristige Stabilität in Meerwasser und chemischen Umgebungen.
- Titan widersteht Ermüdung und Rissbildung, auch bei intensiver Beanspruchung.
- Es bleibt bei hohen Temperaturen strukturstabil und bietet eine starke thermische Leistung.
Ideal für komplexe Geometrien
Die Duktilität von Titan ermöglicht den 3D-Druck komplexer Formen, die mit herkömmlichen Methoden nur schwer herzustellen sind. Es ermöglicht auch interne Kanäle und Gitter durch Topologieoptimierung, was die Leistung steigert.
Sektor | Eigenschaften | Anträge |
Luft- und Raumfahrt | Korrosionsbeständigkeit Hohes Verhältnis von Festigkeit zu Gewicht Hitzebeständigkeit | Flugzeugzellen- und Flügelstrukturen, Verdichterschaufeln, Rotoren und andere Turbinentriebwerksteile |
Medizinisch | Ausgezeichnete Festigkeit Biokompatibilität (ungiftig, nicht allergen) | Orthopädische Hilfsmittel wie Wirbelsäulen-, Hüft- und Knieimplantate |
Automobil & Rennsport | Korrosionsbeständigkeit Hohes Verhältnis von Festigkeit zu Gewicht Hitzebeständigkeit | Bremssättel, Halterungen, Felgen und Ständer |
Vorteile des Titan-3D-Drucks
In der Luft- und Raumfahrt trägt der 3D-Druck von Titan dazu bei, das Buy-to-Fly-Verhältnis zu reduzieren – ein Begriff, der das Gewicht des gekauften Rohmaterials im Vergleich zum Gewicht des endgültigen Teils beschreibt.
Mit herkömmlichen Methoden können Titanteile ein Buy-to-Fly-Verhältnis von 12:1 bis 25:1 haben. Das bedeutet, dass bis zu 90 % des teuren Materials weggeschnitten und verschwendet werden.
Der Titan-3D-Druck senkt dieses Verhältnis auf etwa 3:1 bis 12:1, wobei nur das für das Teil benötigte Material verwendet wird und nur minimaler Abfall aus den Stützstrukturen erzeugt wird.
Bei teuren Materialien wie Titan führt diese Reduzierung zu erheblichen Einsparungen und höherer Effizienz.
Titan 3D-Druck-Anwendungen
Luft- und Raumfahrt
Für Luft- und Raumfahrtunternehmen trägt der 3D-Druck von Titan dazu bei, das Gewicht von hochbelasteten Strukturen zu reduzieren. Es ist ideal für Düsentriebwerke, Gasturbinen und verschiedene Komponenten der Flugzeugzelle.
Liebherr-Luft- und Raumfahrt & Transportation SAS, ein großer Luft- und Raumfahrtzulieferer, hat Anfang des Jahres mit der Serienproduktion von 3D-gedruckten Bugfahrwerkshalterungen aus Titan für den Airbus A350 XWB begonnen.
Durch den Einsatz des Titan-3D-Drucks reduzierte Liebherr das Gewicht der Halterung um 29 % und erhöhte die Steifigkeit.
Jetzt Kontakt aufnehmen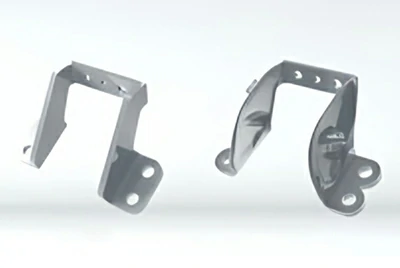
Boeing hat auch eine große Wette auf den 3D-Druck von Titan abgeschlossen. Seit 2015 arbeitet das Unternehmen mit dem norwegischen Metall-3D-Druckunternehmen Norsk Titanium zusammen, um große Titan-Strukturteile für den 787 Dreamliner herzustellen.
Im Jahr 2017 nutzte Boeing die proprietäre Rapid Plasma Deposition (RPD)-Technologie von Norsk, um ein unbenanntes Titanteil herzustellen, das von der U.S. Federal Aviation Administration (FAA) zertifiziert wurde.
3D-gedruckte und bearbeitete Teile von Norsk Titanium
Boeing verwendet die proprietäre Rapid Plasma Deposition (RPD)-Technologie von Norsk zur Herstellung von Titankomponenten.
Jetzt Kontakt aufnehmen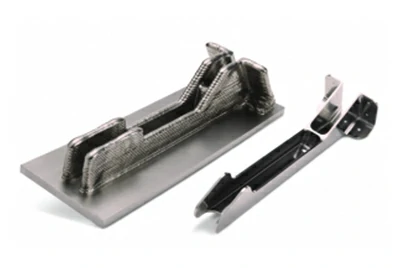
Medizinisch
Im medizinischen Bereich werden 3D-gedruckte Titanimplantate häufig bei Wirbelsäulen-, Hüft-, Knie- und Gliedmaßenoperationen eingesetzt. Sie ermöglichen eine groß angelegte personalisierte Anpassung und verbessern die Patientenergebnisse erheblich.
Osseus Fusion Systems, ein US-amerikanisches Unternehmen, entwickelt solche Geräte. Das 3D-gedruckte Wirbelsäulenimplantat aus Titan, das interkorporelle Fusionsgerät Aries-L, verfügt über ein proprietäres multiplanares Gitter und eine optimierte Mikrooberflächentopologie, die eine schnellere Knochenintegration fördern.
Wirbelsäulenimplantate aus Titan von Osseus
Osseus verwendet den 3D-Druck von Titan, um seine interkorporellen Fusionsgeräte herzustellen.
Jetzt Kontakt aufnehmen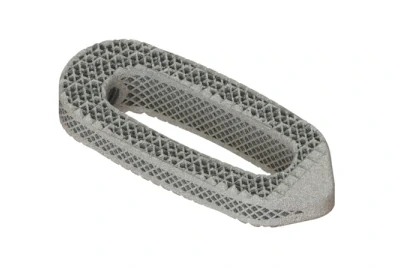
Da immer mehr Medizinhersteller die additive Fertigung in der Produktion einsetzen, wächst die Zahl der von der FDA zugelassenen 3D-gedruckten chirurgischen Implantate auf Titanbasis weiter.
Im Jahr 2023 erhielt ChoiceSpine die FDA-Zulassung für sein Blackhawk Ti, ein 3D-gedrucktes zervikales Zwischenkörper-Abstandshaltersystem aus Titan.
Jetzt Kontakt aufnehmen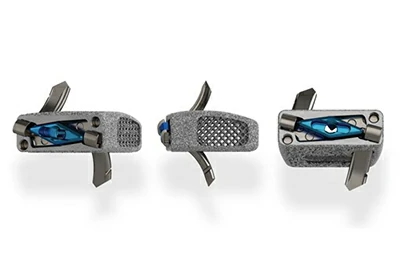
Automobil und Motorsport
Während der 3D-Druck klare Vorteile bietet, ist der Markt für Consumer-Autos sehr kostensensibel, was den Einsatz dieses teuren Materials in den meisten Fahrzeugen einschränkt.
Eine der bemerkenswertesten Anwendungen des Titan-3D-Drucks in der Automobilwelt ist die Entwicklung von Bremssätteln für den Supersportwagen Chiron durch Bugatti.
Bugattis Titan-Bremssattel
Bugattis Titan-Bremssattel
Der Messschieber mit den Maßen 41 x 21 x 13,6 cm wurde in nur 45 Stunden mit der SLM-Technologie 3D-gedruckt.
Jetzt Kontakt aufnehmen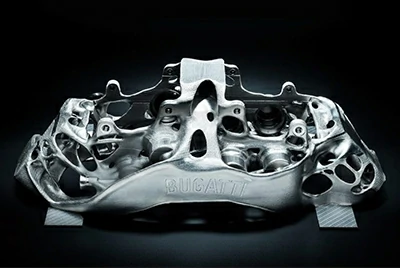
Im vergangenen Jahr testete das Unternehmen den Messschieber erfolgreich und bewies, dass er die Anforderungen an extreme Festigkeit, Steifigkeit und Temperatur erfüllen kann.
Der US-amerikanische Laufradhersteller HRE ist ein weiteres Unternehmen, das vom Titan-3D-Druck profitiert.
Das 3D-gedruckte Titanrad von HRE
HRE nutzte die Laser Powder Bed Fusion (LPBF)-Technologie, um eine komplex geformte Radnabe in 3D zu drucken und dabei eine Gewichtsreduzierung von 19 % zu erreichen.
Jetzt Kontakt aufnehmen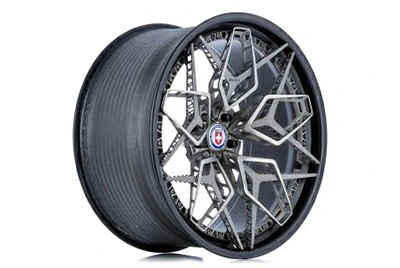
Fahrräder und Konsumgüter
3D-gedrucktes Titan wird häufig in Hochleistungsfahrrädern verwendet – für Rahmen, Kurbeln und Bremshebel – und bietet die Festigkeit von Aluminium, die Leichtigkeit von Kohlefaser und eine bessere Nachhaltigkeit.
Der Fahrradhersteller Ribble hat das Allroad Ti auf den Markt gebracht, das mit einem 3D-gedruckten Titanrahmen ausgestattet ist.
Jetzt Kontakt aufnehmen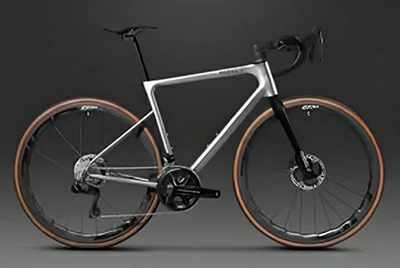
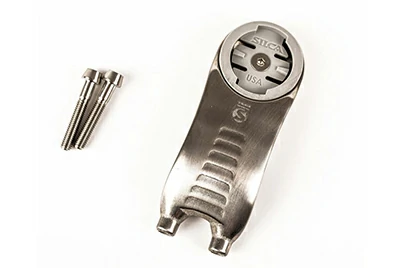
Anfang dieses Jahres brachte Silca seine neueste Linie von 3D-Druckprodukten auf den Markt, darunter eine Reihe von Schaltaugen aus Titan.
Jetzt Kontakt aufnehmenVerve Cycling hat sich mit Metron Additive Engineering zusammengetan, um seine Kurbelgarnitur mittels 3D-Druck neu zu gestalten, das Gewicht zu reduzieren und die Individualisierung zu verbessern.
Jetzt Kontakt aufnehmen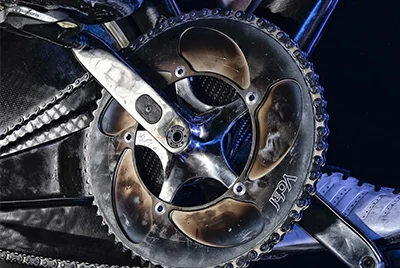
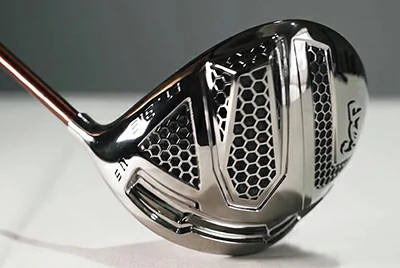
Futai Technology 3D-gedruckter Golfschlägerkopf
Er bietet Golfern eine größere Weite, eine verbesserte Schlagstabilität und eine erhöhte Fehlerverzeihung.
Jetzt Kontakt aufnehmenHerstellung
Der Halbleiterhersteller ASML hat sich aus ganz anderen Gründen dem Titan-3D-Druck zugewandt. Die Titan-Wafer-Trägerschalen werden jetzt in 3D gedruckt statt geschmiedet, was eine Einsparung von 64 % an Rohmaterial und eine Beschleunigung der Lieferung bedeutet.
Norsk Titanium, ein Unternehmen für additive Fertigung von Metallen, verwendete eine DED-Plattform (Directed Energy Deposition), um einen 80 kg (ca. 176 lbs) endkonturnahen Ti64-Preform für die Herstellung von Halbleiterwafern zu drucken.
Präzisionsprodukte & Elektronik
Der 3D-Druck ermöglicht die Herstellung ultradünner, komplexer und hochpräziser Titanteile und eignet sich damit ideal für Uhrengehäuse wie die von Panerai und Holthinrichs.
Im Jahr 2023 brachte die Smartphone-Marke Honor das faltbare Telefon Magic V2 auf den Markt, das mit einer 3D-gedruckten Scharnierabdeckung aus Titan ausgestattet ist, die leichter ist als die vorherige Aluminiumversion, aber dennoch 150 % stärker.
3D-gedruckte Scharnierabdeckung aus Titan
Laut Honor ist dies der Schlüssel zur reibungslosen und dauerhaften Faltleistung des Produkts.
Jetzt Kontakt aufnehmen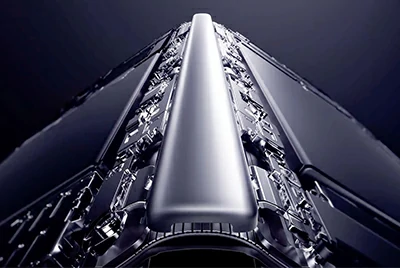
Was sind die wichtigsten Titan-3D-Drucktechnologien?
Laser-Pulverbettschmelzen (LPBF / SLM / DMLS)
Beim Laser-Pulverbettschmelzen (SLM/DMLS/LPBF) wird ein Hochleistungslaser in einer Inertgasumgebung verwendet, um selektiv Schichten aus sphärischem Titanpulver zu schmelzen, die sich schnell verfestigen.
Es ist ideal für kleine bis mittelgroße komplexe Teile mit engen Toleranzen, wie z. B. orthopädische Implantate und Komponenten für die Luft- und Raumfahrt.
SLM, DMLS und LPBF sind markenspezifische Begriffe für im Wesentlichen die gleiche laserbasierte Pulverbett-Fusionstechnologie.
Elektronenstrahl-Pulverbettschmelzen (EBM / EB PBF)
Beim Elektronenstrahl-Pulverbettschmelzen (EBM) wird Titanpulver Schicht für Schicht mit Hilfe eines Elektronenstrahls in einer Vakuumumgebung geschmolzen. Das Verfahren behält eine Hochtemperatur-Bauplattform bei, um Eigenspannungen zu reduzieren und Oxidation zu verhindern.
Es eignet sich für große Implantate und Teile für die Luft- und Raumfahrt, die eine geringe innere Belastung und eine hervorragende Materialqualität erfordern.
Gerichtete Energieabscheidung (DED)
Bei der gerichteten Energieabscheidung (DED) wird ein Laser, ein Elektronenstrahl oder ein Lichtbogen als Wärmequelle verwendet, um Titanpulver oder -draht direkt in einem Schmelzbad zu schmelzen und das Material Spur für Spur abzuscheiden.
Er bietet hohe Abschmelzraten und ist ideal für die Herstellung oder Reparatur von großen Teilen bis zu einer Größe von einem Meter. Drahtrohstoffe können zur Senkung der Materialkosten eingesetzt werden.
Zu den wichtigsten DED-Varianten gehören Electron Beam Additive Herstellung (EBAM), Laser Metal Deposition (LMD/LENS) und Wire Arc Additive Herstellung (WAAM).
Binder-Jetting
Beim Binder Jetting wird ein flüssiges Bindemittel auf Schichten aus Titanpulver gesprüht, um ein "grünes Teil" zu bilden, das später gesintert wird, um die volle Dichte zu erreichen.
Dieses Verfahren ermöglicht den schnellen Druck und die Serienproduktion einfacherer geometrischer Teile und eignet sich daher für die Fertigung in mittleren Stückzahlen.
Lithographiebasierte Metallherstellung (LMM)
LMM baut grüne Teile, indem lichtempfindliches Harz, das Schicht für Schicht mit Titanpulver vermischt ist, mit Licht aushärtet.
Das Harz wird dann durch Sintern entfernt, wodurch das endgültige Teil verdichtet wird. LMM ermöglicht eine Auflösung im Mikrometerbereich und ist ideal für die Herstellung hochdetaillierter, kleiner Teile wie Mikrokanäle und MEMS-Bauelemente.
Prozesse mit hoher Abscheiderate (RPD, Cold Spray, etc.)
Rapid Plasma Deposition (RPD) und Cold Spray sind additive Fertigungsverfahren mit hoher Abscheidungsrate für große Titanteile. RPD verwendet einen Plasmastrahl, um Titandraht für einen effizienten Aufbau zu schmelzen – perfekt für strukturelle Luft- und Raumfahrtteile wie Balken und Fahrwerke.
Cold Spray hingegen treibt feste Metallpartikel mit Überschallgeschwindigkeit an, um sich bei Raumtemperatur zu verbinden, praktisch ohne Wärmeeinflusszone. Es wird häufig für Reparaturen vor Ort oder für dickwandige Konstruktionen verwendet.
Diese Verfahren sind hocheffizient für die Herstellung von Teilen mit einer Größe von mehr als einem Meter, obwohl sie in der Regel eine Nachbearbeitung für die Oberflächenpräzision erfordern.
Nachbearbeitungstechniken für 3D-gedruckte Titanlegierungen
Nach dem Druck ist die Nachbearbeitung unerlässlich, um die erforderlichen mechanischen Eigenschaften und die Oberflächengüte zu erreichen. Im Folgenden sind die gebräuchlichsten Nachbearbeitungsmethoden für Titanlegierungen aufgeführt.
Wärmebehandlung
Die Wärmebehandlung verbessert die mechanischen Eigenschaften wie Festigkeit, Zähigkeit und Ermüdungsbeständigkeit erheblich. Es wird häufig auf hochbeanspruchte Strukturbauteile angewendet.
Zum Beispiel kann Ti-6Al-4V (Ti64) nach der Wärmebehandlung eine Streckgrenze von über 950 MPa und mit HIP sogar über 1000 MPa erreichen, während eine Dehnung von 9 bis 15 % und eine hervorragende strukturelle Stabilität beibehalten werden.
Heißisostatisches Pressen (HIP)
HIP kombiniert hohe Temperaturen und Druck, um die innere Porosität aus dem 3D-Druckprozess zu eliminieren und die Dichte und innere Festigkeit zu verbessern.
Der Prozess läuft in der Regel bei etwa 1000 °C in einer Vakuum- oder Argonatmosphäre für etwa eine Stunde ab.
HIP-behandelte Titanteile können eine Schmiededichte von nahezu 99,5 % mit deutlich verbesserter Dehnung und Zähigkeit erreichen.
CNC-Präzisionsbearbeitung
Während der 3D-Druck Designfreiheit bietet, erfordern hochpräzise Merkmale – wie Passflächen, Gewindebohrungen und Dichtungsnuten – immer noch eine CNC-Bearbeitung, um enge Toleranzen einzuhalten.
Techniken der Oberflächenveredelung
- Polieren: Erzeugt eine spiegelnde Oberfläche, wie sie bei medizinischen Geräten und hochwertigen dekorativen Teilen üblich ist.
- Tumbling: Entfernt Grate in der Serienproduktion und hinterlässt eine gleichmäßig matte Oberfläche.
- Sandstrahlen und Honen: Verbessern Sie die Haftung von Beschichtungen oder erzielen Sie feine Texturen.
Diese Behandlungen verbessern die Haptik, die Korrosionsbeständigkeit und die funktionelle Anpassungsfähigkeit von Titanteilen.
Überblick über Titanlegierungen für den 3D-Druck
Bei der Auswahl einer Legierung ist es wichtig, Faktoren wie Belastung, Temperatur, Korrosionsumgebung und Biokompatibilität zu berücksichtigen. So maximieren Sie sowohl die Designfreiheit als auch die Materialvorteile, die die additive Fertigung bietet.
Legierung | Hauptmerkmale | Hauptanwendungen |
Ti-6Al-4V (Klasse 5) | Am weitesten verbreitete α+β Titanlegierung; Hervorragendes Verhältnis von Festigkeit zu Gewicht und Korrosionsbeständigkeit | Strukturen für die Luft- und Raumfahrt, Hochleistungsteile, allgemeine medizinische Geräte |
Ti-6Al-4V ELI (Klasse 23) | Extra niedrige interstitielle Version der 5. Klasse; ausgezeichnete Biokompatibilität | Orthopädische Implantate, Zahnimplantate, individuelle Prothesen |
Ti-5Al-5V-5Mo-3Cr (Ti-5553) | Hochfestes β-Titan mit ausgezeichneter Kriechfestigkeit und Zähigkeit | Fahrwerke, Triebwerksgehäuse, militärische Hochlaststrukturen |
Ti-6Al-2Sn-4Zr-2Mo (Ti-6242) | Hervorragende Leistung bei hohen Temperaturen bei gleichbleibender Festigkeit | Heiße Sektionen von Düsentriebwerken, Komponenten für Rennmotoren |
Ti-3Al-2.5V (Klasse 9) | Mittlere Festigkeit mit guter Schweißbarkeit und Korrosionsbeständigkeit | Chemie-, Öl- und Gasrohrleitungen, Fahrradrahmen |
β21S (Ti-15Mo-3Nb-3Al-0.2Si) | Fortschrittliches β-Titan; hohe Festigkeit, Kriech- und Oxidationsbeständigkeit | Düsentriebwerke, kieferorthopädische Brackets, orthopädische Befestigungselemente |
TA15 (Ti-6Al-2Zr-1Mo-1V) | Nahezu α Titan mit hoher spezifischer Festigkeit und thermischer Stabilität | Hochtemperatur-Tragrahmen, Flugzeughautverstärkungen |
3D-Drucker für Titan
Laser-Pulverbettschmelzen (LPBF / SLM / DMLS)
- EOS:M 290,M 400-4
- GE Additiv / Kolibrium-Additiv: M2 Serie 5, M Linie
- Nikon SLM-Lösungen: NXG X12, NXG 600
- 3D-Systeme: DMP Flex 350, Fabrik 500
- Velo3D: Saphir, Saphir XC
- TRUMPF:TruPrint 2000,3000,5000
- Renishaw:RenAM 500 Serie
- Hinzufügen:FormUp 350
Elektronenstrahl-Pulverbettschmelzen (EBM / EB PBF)
GE Additive Arcam: Q10 Plus, Q20 Plus, Spectra H
Gerichtete Energieabscheidung (DED)
- Sciaky: EBAM 110, EBAM 300 (Elektronenstrahl + Titandraht)
- MELD-Fertigung: MELD L-Serie (Festkörper-Reibungsabscheidung mit Titanstäben oder -stäben)
Binder-Jetting
- Desktop-Metall: Produktionssystem P-50, X-Serie
- Desktop Metal P-1: Erfordert ein "Reactive Safety Kit" zur Unterstützung von reaktiven Materialien wie Titan und Aluminium
- Markgeschmiedet: PX100
Herstellung von Metallschmelzfilamenten (Metall FFF / BMD)
Desktop Metal: Studio System 2 (BMD-Technologie mit dediziertem Ti-6Al-4V-Filament)
Kaltspritzen – Festkörper-Hochgeschwindigkeits-Abscheidungstechnologie
Spee3D:WarpSPEE3D
Kosten für Titan 3D-Drucker
Die Kosten sind ein Schlüsselfaktor, den viele Unternehmen bewerten müssen, bevor sie den Titan-3D-Druck einführen.
Hohe Anfangsinvestition
- 3D-Drucker aus Titan in Industriequalität kosten in der Regel zwischen 250.000 und 1.000.000 US-Dollar.
- Hochreines, kugelförmiges Titanlegierungspulver kostet etwa 300 bis 600 US-Dollar pro Kilogramm.
- Viele Unternehmen entscheiden sich für die Zusammenarbeit mit 3D-Druck-Dienstleistern. Die endgültigen Druckkosten betragen oft ein Vielfaches der Materialkosten, abhängig von der Komplexität des Teils und den Anforderungen an die Nachbearbeitung.
Warum es sich trotzdem lohnt, zu investieren
- Leichte, hochfeste Materialien reduzieren das Gewicht des Flugzeugs, sparen Treibstoff und erhöhen die Reichweite – was zu langfristigen Einsparungen bei den Betriebskosten führt.
- Die Biokompatibilität von Titan und die Designflexibilität des 3D-Drucks ermöglichen Implantate, die besser zu einzelnen Patienten passen, was die chirurgischen Ergebnisse verbessert und den Bedarf an Revisionsoperationen reduziert.
- Titanlegierungen bieten eine hervorragende Ermüdungsbeständigkeit bei hohen Temperaturen und eignen sich daher ideal für kritische Teile in Düsentriebwerken, Raketenstrukturen und Rennkomponenten.
Der 3D-Druck von Titan ist nicht nur eine Fertigungsmethode, sondern eine treibende Kraft für Leistungssteigerungen und Designfreiheit.
In Branchen mit anspruchsvollen Umgebungen, individuellen Anforderungen oder strengen Leichtbauzielen überwiegt der Wert in Bezug auf Materialleistung, Strukturoptimierung und Betriebseffizienz die Anschaffungskosten bei weitem.
Herausforderungen des 3D-Drucks: Die technischen Barrieren hinter hoher Leistung
Mangel an einheitlichen Standards und Zertifizierungen
Derzeit sind die Standards für die Kombination von Titan mit der additiven Fertigung noch unterentwickelt. Dies stellt in Hochrisikobranchen wie der Luft- und Raumfahrt und der Medizintechnik ein Hindernis dar.
So hat Boeing beispielsweise bereits 2018 eine Partnerschaft mit Oerlikon geschlossen, um an der Standardisierung des Titan-3D-Drucks zu arbeiten, um die Flugsicherheitsanforderungen der FAA (Federal Aviation Administration) und des DoD (Department of Defense) zu erfüllen.
Hohe Kosten für Titanpulver
Titanpulver für den 3D-Druck muss eine hohe Reinheit, eine hervorragende Sphärizität und eine gleichmäßige Partikelgrößenverteilung aufweisen. Die Herstellung erfordert viel Energie und strenge Kontrolle, wodurch die Preise hoch bleiben – in der Regel um die 300 bis 600 US-Dollar pro Kilogramm.
Komplexe Temperierung und Wärmemanagement
Mit einem Schmelzpunkt von 1668 °C erfordert Titan eine präzise thermische Kontrolle während des Drucks.
Unsachgemäßer Wärmeeintrag kann zu inneren Spannungen, Verformungen oder Rissen führen, die die strukturelle Integrität und Lebensdauer stark beeinträchtigen können – besonders wichtig für Luft- und Raumfahrt- und Implantatanwendungen.
Schwierigkeiten beim Erreichen eines gleichmäßigen Sinterns und einer gleichmäßigen Dichte
Die mechanische Leistung von Titanteilen hängt stark von der Gleichmäßigkeit und Dichte ab, die beim Sintern oder Schmelzen erreicht wird.
Porosität, Einschlüsse oder mikrostrukturelle Inkonsistenzen können zu Spannungskonzentrationen und potenziellen Versagensstellen führen, insbesondere beim Drucken komplexer Geometrien.
Herausforderungen bei der Konstruktion und Demontage von Stützstrukturen
Der 3D-Druck von Titan erfordert oft starke, komplizierte Stützstrukturen, um einen Zusammenbruch oder eine Verformung bei hohen Temperaturen zu verhindern.
Nach dem Druck müssen diese Stützen präzise entfernt werden, ohne das Teil zu beschädigen – eine zusätzliche Komplexität im Gesamtprozess.
Übersicht über Lieferanten von Titan und Titanlegierungspulver
Chalco Titan
Als führender Titanlieferant in China baut Chalco Titan sein Geschäft mit Titanlegierungspulvern für die additive Fertigung aktiv aus.
Das Unternehmen bietet sowohl Titanwerkstoffe in Industrie- als auch in Luft- und Raumfahrtqualität, unterstützt die Entwicklung kundenspezifischer Legierungen und bietet eine kostengünstige Massenversorgung für die Luft- und Raumfahrt-, Medizin- und Automobilmärkte weltweit. Schnelles Angebot
Zimmermannstechnik
Bietet Ti-6Al-4V ELI-Legierungspulver (Klasse 23) für die Medizin- und Luft- und Raumfahrt mit einem gut etablierten Zertifizierungssystem an. Umfassend beliefert Hersteller von medizinischen Implantaten, orthopädischen und zahnärztlichen Geräten.
IperionX
Ein in den USA ansässiger Anbieter, der sich auf nachhaltiges Titanrecycling konzentriert. Entwickelt umweltfreundliche Titanpulver für den 3D-Druck und fördert kohlenstoffarme additive Fertigungslösungen.
Sandvik / Fischadler
Bietet zertifizierte Osprey Ti-6Al-4V Pulver der Klassen 5 und 23 mit konsistenter Chargenkontrolle. Weit verbreitet in der Luft- und Raumfahrt und in medizinischen Anwendungen.
AP&C (Colibrium Additive, Teil von GE Additive)
Ein weltweit anerkannter Marktführer im Bereich der Zerstäubung von Titanpulver. Die Produkte des Unternehmens unterstützen sowohl Laser- als auch Elektronenstrahl-additive Fertigungsverfahren.
Titan 3D-Druck-Service
Für die meisten Unternehmen oder Privatanwender ist der Kauf eines teuren Metall-3D-Druckers zur Herstellung von Titanteilen nicht praktikabel. Glücklicherweise gibt es jetzt viele ausgereifte Titan-3D-Druckdienste von Drittanbietern, um hochwertige Metallteile schnell und effizient zu liefern.
Bei der Auswahl eines Druckdienstes ist es wichtig, die Art der angebotenen Titanlegierung (z. B. Ti-6Al-4V oder kommerziell reines Titan) zu bestätigen. Einige Spezialsorten, wie z. B. CP-Ti- oder ELI-Versionen, erfordern möglicherweise Sonderanfertigungen oder zusätzliche Vorlaufzeit.
Auf der weltweit anerkannten On-Demand-Fertigungsplattform Craftcloud können Benutzer beispielsweise einfach eine CAD-Datei hochladen, Titan als Material auswählen und sofortige Angebote von verschiedenen Fertigungspartnern erhalten. Benutzer können dann einen Anbieter basierend auf Preis, Vorlaufzeit oder Standort auswählen.
Heute bieten führende Gerätehersteller wie 3D Systems, EOS und SLM Solutions sowie Pulverlieferanten wie Sandvik und Carpenter Additive auch kundenspezifische Titandruckdienstleistungen an. Diese Dienstleistungen werden häufig in stark nachgefragten Branchen wie Medizin, Luft- und Raumfahrt, Automobil und Werkzeugbau eingesetzt.
Häufig gestellte Fragen zum 3D-Druck von Titan
Wie stark ist 3D-gedrucktes Titan?
Seine Festigkeit kann mit Schmiedeteilen mithalten und eignet sich daher für hochbelastete Strukturbauteile.
Welche Materialien können nicht in 3D gedruckt werden?
Einige hochreaktive Metalle und Verbundwerkstoffe stellen für den kommerziellen 3D-Druck noch eine Herausforderung dar und sind noch nicht weit verbreitet.
Was ist Titan 3D-Drucker Filament?
Es handelt sich um ein Polymerfilament, das mit Titanpulver angereichert ist und in FDM-Metalldruckern verwendet wird.
Wie funktioniert der Titan-3D-Druck?
Es verwendet einen Laser oder Elektronenstrahl, um Titanpulver oder Draht Schicht für Schicht zu schmelzen, um ein Teil zu bilden.
Was ist 3D-Druck von Titanpulver?
Es handelt sich um ein hochreines, kugelförmiges Titanlegierungspulver, das speziell für die additive Fertigung hergestellt wurde.