Titanium Used in Aircraft
With the continuous development of aviation technology, aircraft have put forward higher requirements on materials in terms of structural design and performance indicators. They need to be lightweight to reduce the weight of the aircraft, high strength to ensure structural safety, and excellent corrosion resistance and high temperature resistance to adapt to the complex and changing flight environment. Titanium alloys can meet this demand and are widely used in various parts of aircraft.
Why choose titanium alloy?
- Titanium alloy is light in weight but high in strength, which can effectively reduce the weight of aircraft structure and improve fuel efficiency.
- A stable oxide film is formed on the titanium surface, which can resist corrosion from aviation fuel, seawater and hot and humid environments.
- It performs stably under high cyclic loads, extending the service life of structural parts.
- Some titanium alloys can operate at temperatures above 500°C and are suitable for high-temperature areas of the engine.
Titanium alloy parts for aircraft
Aircraft structural components
Aircraft structural parts such as fuselage frames, floor beams, wing box structures, engine pylons and other key load-bearing components need to have high strength, fatigue resistance, corrosion resistance and other characteristics. Due to the widespread application of composite materials, the materials of these structural parts must also be highly matched with composite materials in terms of electrochemical properties and thermal expansion coefficients to avoid corrosion and thermal stress.
Body frame
The fuselage frame is made of titanium alloy Ti-6Al-4V. As the skeleton of the aircraft structure, the fuselage frame bears the overall load and the internal and external pressure difference, so the material needs to have a very high strength-to-weight ratio, excellent fatigue resistance and good corrosion resistance.
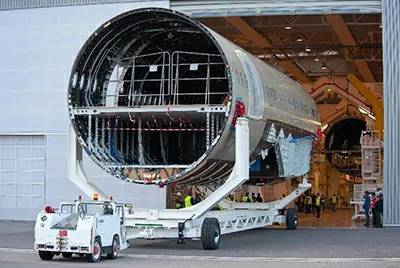
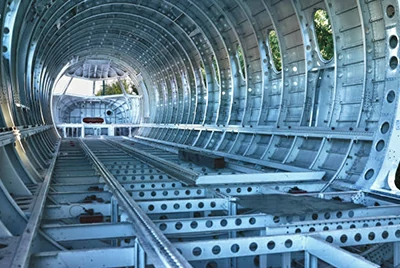
Floor beams
The floor beam is made of titanium alloy Ti-6Al-4V. As a key structural component that bears the weight of the cabin and cargo hold, the floor beam requires high strength, high rigidity and excellent fatigue resistance.
Wing box structure
Ti-6Al-4V alloy is widely used in the basic components of wing box structures, while Ti-5553 alloy is mainly used in the connection nodes and reinforcement structures of wing boxes due to its excellent hardenability and fatigue resistance.
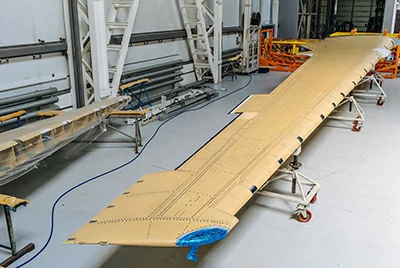
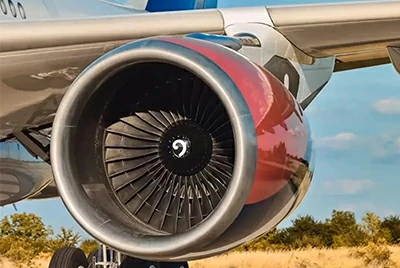
Engine mount
The engine mount needs to bear engine thrust, vibration and high impact loads, so the material must have extremely high strength and fatigue resistance. Ti-5553 alloy has become the first choice for engine mount structural materials due to its high strength, good toughness and crack resistance.
Why choose the following alloys for aircraft structural parts:
The key requirements for materials for aircraft structural parts include high strength, light weight, fatigue resistance, corrosion resistance and compatibility with composite materials.
Ti-6Al-4V alloy has comprehensive performance advantages and is suitable for most structural parts. Especially when used in conjunction with composite materials, it can significantly improve structural durability and reduce maintenance costs.
Ti-5553 alloy is a new type of high-performance titanium alloy with good thick section hardenability, outstanding fatigue resistance and fracture toughness, and is suitable for complex load environments.
Application examples:
In actual applications, Ti-6Al-4V alloy is widely used in the fuselage frame, floor beams and wing box structures of the Boeing 787 Dreamliner, which accounts for more than 15% of the total weight of the aircraft.
The Airbus A350 XWB's engine pylons and wing box connection structures make extensive use of Ti-5553 alloy, which greatly improves the overall performance and service life of the aircraft.
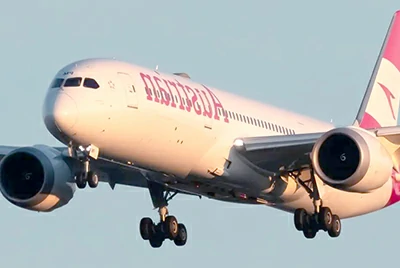
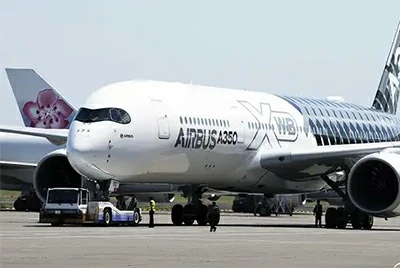
Landing gear system
The landing gear system is a key component that bears high impact loads during aircraft takeoff, landing and taxiing. It has a complex structure and requires extremely high material strength, toughness and corrosion resistance. Titanium alloy is widely used in modern aircraft landing gear due to its high strength and weight advantages.
Main landing gear strut
The main landing gear strut is the most important load-bearing component in the landing gear system and needs to withstand strong impact from the ground. Ti-10V-2Fe-3Al alloy has high strength and good fracture toughness, making it the core material for the landing gear of modern large passenger aircraft.
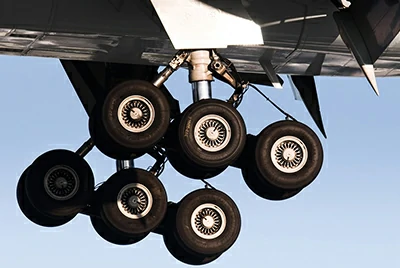
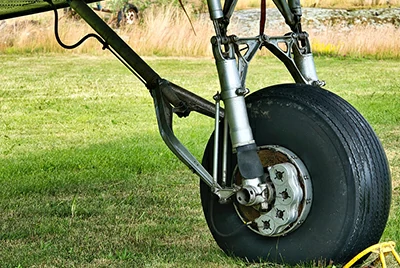
Steering bracket and side support rod
The side support rod and steering structure connect the landing gear to the fuselage and need to have certain flexibility and long-term load-bearing capacity. Ti-5553 alloy is suitable for these high fatigue load parts due to its good comprehensive mechanical properties.
Why choose the following alloys for landing gear?
The landing gear material needs to have high strength and excellent fatigue resistance to withstand the impact of frequent take-offs and landings and ensure safety and reliability.
Ti-10V-2Fe-3Al alloy can significantly reduce structural weight and extend the service life of the landing gear due to its high strength and outstanding fatigue resistance.
Ti-5553 alloy is suitable for high load and high fatigue conditions, has excellent hardenability and mechanical properties, and can meet the performance requirements of landing gear under complex loads.
Application examples:
The landing gear systems of Boeing 777, 787 and Airbus A350 use Ti-10V-2Fe-3Al as the main support material, and Ti-5553 is used for support rods, hinged components and other structures, effectively reducing the weight of the entire aircraft while ensuring high reliability.
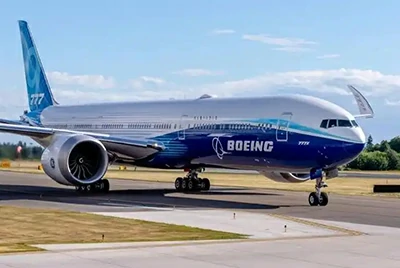
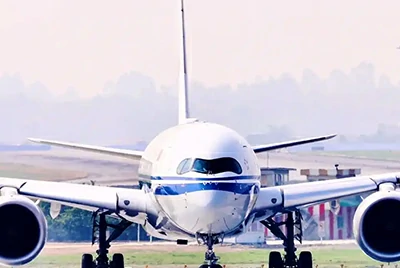
Engine Components
Aircraft engine components need to withstand high temperatures, high pressures and high-speed rotations for a long time, and the materials must maintain stable mechanical properties and fatigue resistance in extreme environments. Titanium alloys play an important role in many key engine components due to their good high-temperature strength and light weight.
Fan blades and fan discs
Fan blades and fan disks are located in the low-temperature front section of the engine, and require materials with high strength and corrosion resistance at medium temperatures. Ti-6Al-4V alloy meets the above requirements and is widely used in fan components of medium and large turbofan engines.

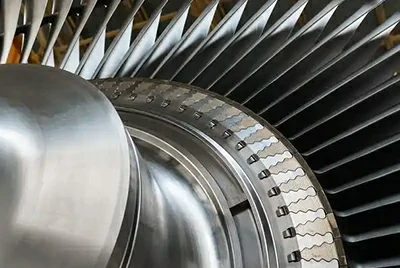
Compressor disks and blades
The operating temperature of high-pressure compressor parts can reach above 500°C, requiring the material to have high-temperature strength, good creep performance and low-cycle fatigue performance. Ti-6246 and Ti-8Al-1Mo-1V are α+β type titanium alloys with excellent high-temperature performance, which are widely used in the compressor structure of the core section of the middle part of the engine.
Engine housing and rings
Engine casings and rings must have good dimensional stability and meet certain high temperature and welding performance requirements. Ti-5Al-2.5Sn alloy has both medium temperature strength and good weldability, and is suitable for compressor casings and other parts.
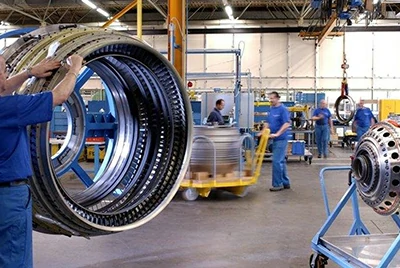
Material requirements for engine components and reasons for alloy selection
Engine components have stringent requirements on materials, including maintaining high strength at medium and high temperatures, corrosion resistance and excellent fatigue resistance.
Ti-6Al-4V alloy has high strength and corrosion resistance at medium temperature conditions and is suitable for fan structures.
Ti-6246 and Ti-8Al-1Mo-1V alloys have excellent heat resistance and fatigue resistance, meeting the high requirements of compressor components.
Ti-5Al-2.5Sn alloy has good welding performance and stable dimensions, and is suitable for engine housing manufacturing.
Application examples:
The fan blades of the Rolls-Royce Trent 1000 engine are made of Ti-6Al-4V, the compressor section uses Ti-6246 and Ti-8Al-1Mo-1V alloys, and the engine casing uses Ti-5Al-2.5Sn, achieving a balance between lightweight and high thermal strength.
Hydraulic and fuel systems
Aircraft hydraulic and fuel systems involve high-pressure transmission and complex piping structures, requiring materials to have high strength, good weldability and corrosion resistance.
Hydraulic lines
Hydraulic systems are often used in high-pressure transmission circuits, and pipelines need to withstand pressures greater than 3000 psi. Ti-3Al-2.5V, as an α+β type titanium alloy, has good strength, ductility and pressure resistance, and is the preferred material for hydraulic pipes.
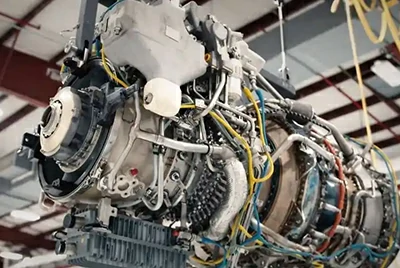
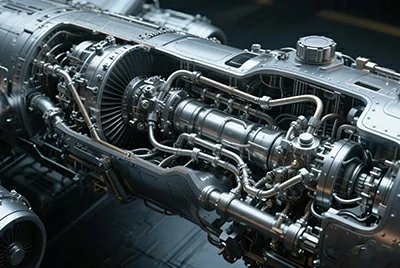
Fuel and gas delivery pipes
Commercially pure titanium is often used for welded pipes that carry fuel and cooling gas because of its excellent corrosion resistance. Grade 2 is more formable and Grade 4 is stronger.
Material requirements and reasons for alloy selection:
Materials need to have both strength and flexibility to ensure reliable operation of high-pressure hydraulic systems.
Ti-3Al-2.5V alloy combines strength and flexibility, suitable for high-pressure hydraulic systems.
Pure titanium (CP Ti) has excellent corrosion resistance and good processing performance, and is suitable for lightweight piping systems.
Application examples:
In the hydraulic and fuel systems of Boeing 787 and Airbus A350, Ti-3Al-2.5V high-pressure seamless pipes and Grade 2 pure titanium welded pipes are widely used to effectively ensure the system pressure and corrosion resistance requirements.
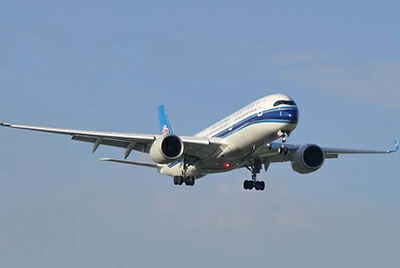
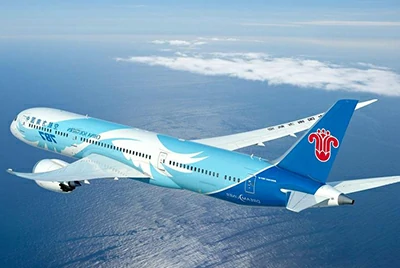
Fasteners and Small Parts
The connections between aircraft components rely on a large number of fasteners, which must be high-strength, corrosion-resistant, lightweight, and able to withstand alternating loads for a long time.
Bolts, Nuts & Rivets
Bolts, nuts and rivets are made of titanium alloys, including Ti-6Al-4V, Ti-6Al-2Sn-4Zr-2Mo and SPS TITAN™ series. Titanium fasteners can replace traditional steel parts, reducing weight by an average of 30% to 40%. Among them, Ti-6Al-4V is the most commonly used general material, and the SPS TITAN™ series is designed for extreme working conditions.
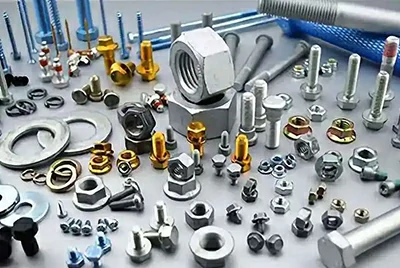
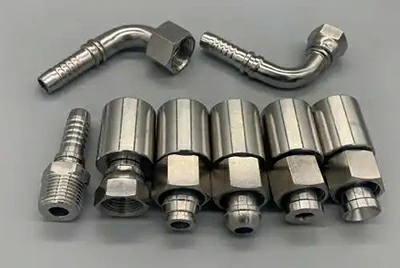
Connectors and small parts
Connectors and small parts are made of titanium alloy Ti-3Al-2.5V and pure titanium (CP Ti). In aircraft hydraulic joints, small brackets and electronic compartment components, titanium alloys are widely used in the manufacture of precision small parts due to their excellent corrosion resistance and lightweight advantages.
Material requirements and reasons for alloy selection
Ti-6Al-4V and Ti-6-2-4-2 alloys have high strength and good fatigue properties, and are suitable for long-term service of connectors.
SPS high-strength titanium alloy meets the triple requirements of high strength, corrosion resistance and fatigue resistance, and is suitable for more demanding working conditions.
Why choose Chalco as your aerospace grade titanium supplier?
Equipment Strength
Chalco has a complete and modern titanium smelting and processing production line, covering the entire process from titanium ingot smelting to precision forging, heat treatment and testing, ensuring that it can provide global customers with titanium alloy products that meet international aviation standards.
It is equipped with multiple vacuum consumable arc furnaces (VAR), with the maximum ingot diameter of 1000mm and a single ingot weight of 6 tons; it is also equipped with plasma melting furnace (PAM) and electron beam melting furnace (EB) to meet the smelting needs of high-purity aviation titanium ingots and special alloys.
It has an 8,000-ton die forging press and isothermal forging system, supporting ring rolling mills and hot die forging production lines, which can accurately manufacture key aviation structural forgings such as landing gear struts, discs, frame connectors, etc.
Equipped with multiple aviation-specific vacuum heat treatment furnaces and annealing furnaces, the temperature control accuracy is ±2°C, and the maximum processing size is 2.5 meters, ensuring that the organizational uniformity and mechanical properties meet the aviation fatigue and thermal stability requirements.
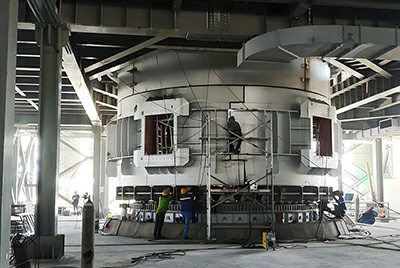
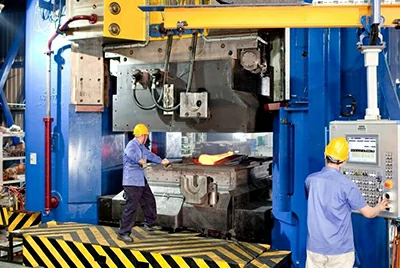
Quality assurance
In order to ensure that its products meet aviation-grade standards, Chalco has established a strict quality control system that covers every link from raw materials, production process to final delivery.
All aviation titanium alloy products must undergo a complete non-destructive testing process before leaving the factory, including ultrasonic testing (UT), X-ray testing and surface crack inspection to ensure that there are no internal defects, pores or inclusions, and to meet the safety performance requirements of aircraft structures and engine components.
Chalco has a complete physical and chemical experimental platform that can conduct metallographic structure analysis, tensile performance testing, high temperature performance evaluation, fatigue life testing and creep rupture testing, providing reliable process traceability and performance assurance for each batch of aviation titanium materials.
The company's laboratory has passed the AS9100 international aviation quality management system certification and obtained NADCAP heat treatment and non-destructive testing certification. It has the ability to provide a full set of material certificates (MTC) and third-party test reports to international aviation customers to ensure that exported materials meet the quality requirements of major manufacturers such as Boeing and Airbus.
Chalco can provide other aviation grade products
What services can Chalco provide for you?
As a professional manufacturer of aviation-grade titanium alloy materials, Chalco not only provides high-quality titanium products, but is also committed to providing global customers with one-stop titanium alloy solutions, with efficient collaboration throughout the entire process from material selection to delivery.
Material customization
According to customer application requirements (aircraft structure, engine, hydraulic system, etc.), we provide suitable titanium alloy grade recommendations (such as Ti-6Al-4V, Ti-5553, Ti-6246, etc.), and support customized chemical composition, heat treatment status, and mechanical property standards.
Multi-specification product processing services
Chalco can supply titanium alloy bars, plates, forgings, rings, forging rings, connectors, etc. with high dimensional accuracy, supporting rough machining and near-net forming processes for special-shaped parts, meeting the early processing needs of aviation structural parts.
Material testing and third-party certification
Each batch of materials comes with a full set of factory inspection reports and MTC certificates, and supports witness inspections by third-party inspection agencies such as BV, SGS, and TÜV to ensure that the products meet international procurement standards.
Small batch test
It supports small batch R&D testing, sample proofing, and batch supply switching, with short delivery cycle and rapid response to customer project rhythm. It is suitable for the trial production stage, long-term supply and alternative material development.
International trade and logistics services
Chalco's experienced foreign trade team can provide a variety of trade methods such as EXW, FOB, CIF, etc. They are familiar with the customs clearance and packaging requirements for aviation materials exported to North America, Europe, the Middle East, and Southeast Asia, ensuring transportation safety and stable delivery time.